取材・写真・文/大草芳江
2020年01月30日公開
産業技術総合研究所東北センター(以下、産総研東北センター)が東北地域新産業創出に向けて、産学官金"協奏"による新たな企業支援の試み「Tohoku Advanced Innovation Project(TAIプロジェクト)」を2018年夏からスタートさせた。産業・技術環境の変革の波に乗って企業が大きく発展できるよう、主に経営層を対象に、さまざまな先端技術を体験できる勉強会「EBIS(Expanding Business Innovations for executiveS)ワークショップ」を開催している。2019年度に東北各県で実施されたEBISワークショップの模様をレポートする。
【関連記事】
◆ 産総研「TAI(鯛)プロジェクト」始動!~東北発イノベーションに向けて~
◆ 第1回産総研EBISワークショップレポート「中小企業のIT化からIoT化を支援するMZプラットフォームセミナー」
◆ 第2回産総研EBISワークショップレポート「青森県よろず支援拠点IoT活用セミナー」
◆ 第3回産総研EBISワークショップレポート「わが社で使える放射光」
◆ 第4回産総研EBISワークショップレポート「エッジAIがビジネスを変える」
◆ 第5回産総研EBISワークショップレポート「チームの創発力・実現力を引き出すデザインブレインマッピング(新規事業創出に向けて)」
※ 本インタビューをもとに産業技術総合研究所様「TAIプロジェクト報告書」を作成させていただきました。詳細は、産業技術総合研究所東北センターHP「TAIプロジェクト」をご覧ください。
2019年度 産総研東北センターTAIプロジェクト EBISワークショップ「ハーネスの未来~100年に1度の変革期に備えるには~」レポート
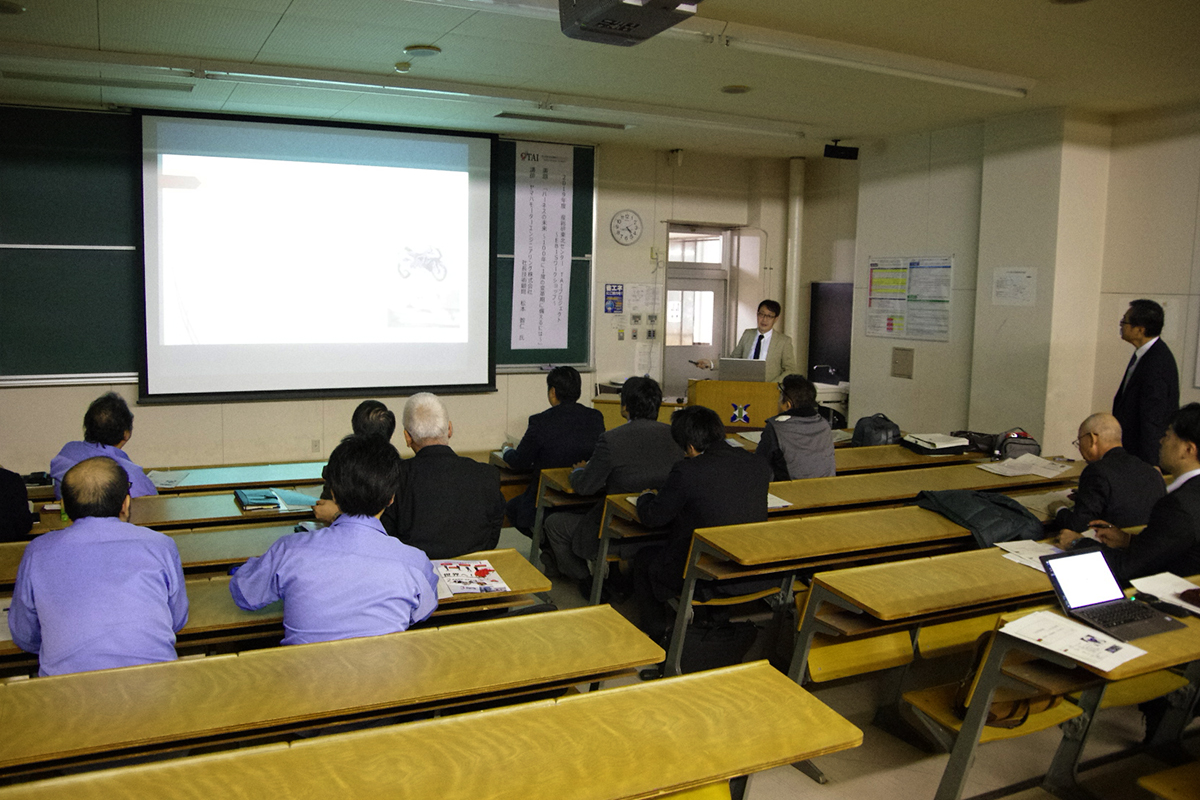
「ハーネスの未来~100年に1度の変革期に備えるには~」のようす=11月28日、八戸工業大学(青森県八戸市)
自動車業界は現在、「CASE(コネクテッド、自動運転、シェアリング、電動化)」と呼ばれる100年に1度の変革期を迎えている。CASEに象徴される新技術普及を背景に、「ハーネス」(複数の電線を束にした部品)の今後を考える勉強会「ハーネスの未来~100年に1度の変革期に備えるには~」が11月28日、八戸工業大学(青森県八戸市)にて開催され、中小企業や支援機関等の担当者ら10名が参加した。
新たな事業の柱につながる気づきの場を企業に提供しようと、産業技術総合研究所(以下産総研)東北センターが昨年度から推進するプロジェクト「TAIプロジェクト」(Tohoku Advanced Innovation Project)の一環。東北地域の中堅・中小企業の経営者等を対象に、講師との議論や新しい技術の体験に重点を置いた勉強会「EBIS(Expanding Business Innovation for executiveS)ワークショップ」を様々なテーマで開催している。
勉強会では、はじめに主催者の産総研東北センターの井ノ上俊宏さんが趣旨説明を行い、「自動車向けのハーネスには、安全制御や自動運転等を背景に高速化対応が求められ、固定設備向けハーネスについては無線化の動き等、ハーネス業界も大きな技術変革期にある。100年に1度の変革期に早めに備えていただきたい」と話した。
続けて、講師を務めたヤマハモーターエンジニアリング株式会社(静岡県磐田市)の松本智仁さんが「つながる技術 ハーネスの未来~移動体・FA産業機器ハーネスの状況~」と題して講演を行った。松本さんは自動車や産業機器等の配線を減らす「CANバス通信」を中心に解説し、ハーネスの今後について「主に国内生産される高付加価値品は、複数の制御の高度化と軽量化、コストダウン等のために、高速通信や無線化へ移行する傾向にある」と語った。
その後、講師と参加者による議論の時間が1時間強設けられ、参加者からは「ハーネスは無くなるか」「ハーネス加工メーカーが今取り組むべきことは」といった活発な質疑応答があった。勉強会の詳細レポートは、以下の通り。
つながる技術 ハーネスの未来 ~100年に1度の変革期に備えるには~
/産業技術総合研究所東北センター イノベーションコーディネータ 井ノ上 俊宏 さん
◆ 車の未来 EV化、安全制御と自動運転
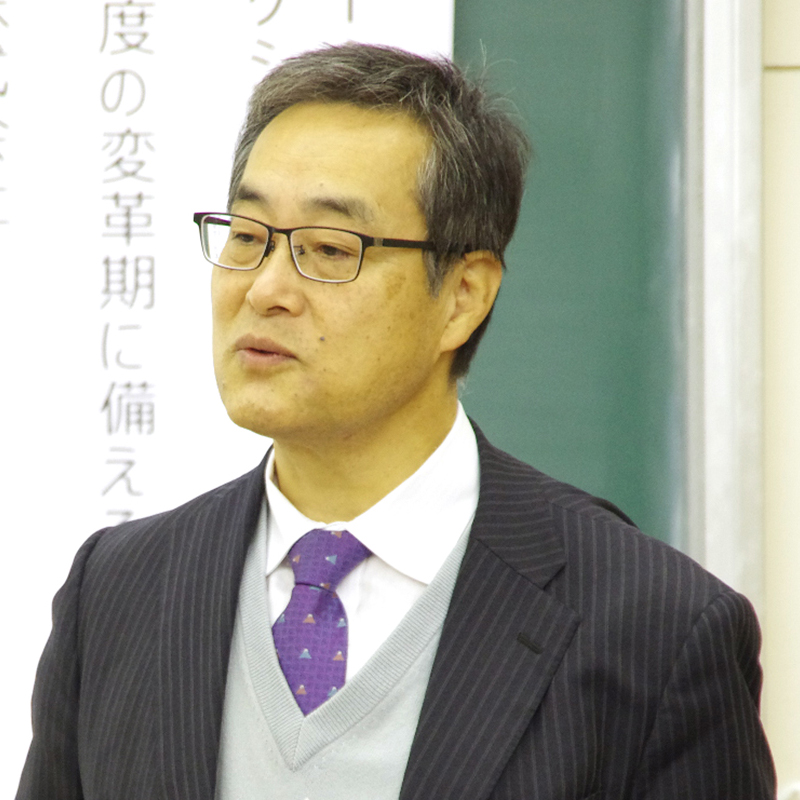
産業技術総合研究所東北センターの井ノ上俊宏さん
ハーネスは現在、主に移動体と固定設備に使われています。まず、移動体のこれからの流れとして、EV(電気自動車)化、安全制御と自動運転があります。そのために必要な情報通信量は現行の毎秒25ギガビット程度では間に合わず、少なくとも現行の4倍の毎秒100ギガビットは必須と言われています。センサで検知してからブレーキをかけるという制御を速やかに行うには、それくらい高速化しなければ衝突してしまうわけです。高速化といえば圧縮・解凍技術もありますが、安全制御と自動運転のスピード要求に耐えることはできません。センサで検知したデータを圧縮して制御基板へ送り、それを解凍してからブレーキへ戻すのでは、間に合わないのです。
このような自動運転化等の流れを背景に、毎秒100ギガビット以上という高速化対応と信頼性の要求を満たす一定の国際規格も、ここ数年のうちに作られるでしょう。国際規格が出てくれば、世の中は一気に進んでいくことが考えられます。高速化を追求すれば、最終的には、全体ではなくとも、メタルの線から光通信や無線へ移行する可能性もあります。
以上のような技術の根本的転換に対して一定の準備をしておかなければ、対応できない、あるいは置いていかれることが起こり得ます。そこでまずは勉強会を開きましょう、というのが本日の趣旨です。
◆ ローカル5G:工事現場や建設現場にも 京セラの挑戦
また、工事現場や建設現場の固定設備等については、京セラが、第5世代通信(5G)を地域限定で利用する「ローカル5G」事業に参入することを、今年11月に公表しました。ベースとなるのは無線技術で、総務省が定めた「5G通信帯域」の基地局設備を自社開発し、2022年には市場投入するそうです。線を使わないため、設置の自由度が高く、安価に設置できることが売りです。京セラは「ローカル5Gの国内市場は数千億円規模になる」と試算しており、京セラのほかにも、富士通やパナソニックといったビックネーム企業が参入に意欲を示しています。
そのような背景の中、本日はヤマハモーターエンジニアリング株式会社様から松本智仁先生にお越しいただき、ご講演いただきます。松本先生は現在、ヤマハモーターエンジニアリング様の社長付き技術顧問をされている方です。ぜひ積極的にご質問ください。?
つながる技術 ハーネスの未来~移動体・FA産業機器ハーネスの状況~
/ヤマハモーターエンジニアリング株式会社 松本 智仁 さん
◆ 親会社のヤマハ発動機株式会社について
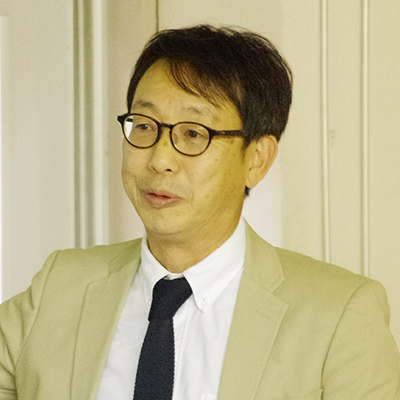
ヤマハモーターエンジニアリング株式会社の松本智仁さん
はじめに、私どもの親会社であるヤマハ発動機株式会社からご紹介します。ヤマハ発動機はパワートレイン技術や制御技術等を利用し、車両の開発、製造、販売を行う会社です。以前は「パワートレイン技術」と言わず「エンジン技術」と称していましたが、電動化が叫ばれる中、制御技術をより活用して商機に結びつけようと、現在はエンジンやモーター等も含める形で事業を行っています。主な事業内容は、モーターサイクル事業やレクリエーショナルビークル事業、マリン事業等です。
◆ ヤマハモーターエンジニアリング株式会社について
私が所属している、ヤマハモーターエンジニアリング株式会社は、ヤマハ発動機株式会社100%出資の子会社です。事業内容は弊社独自商品として、消防機関向けのホースレイヤー等の一部を除いて、多くは親会社であるヤマハ発動機向けのもので、モーターサイクルの開発・実験評価、エンジン開発、特殊車両の開発、制御開発等を担当しています。
◆ BMW 4輪車で約50kg、2輪車で約30kgの軽量化を実現
さて、本題の移動体に使用されるハーネスについてご説明します。皆さんも御存知の通り、大型バイクには非常に長い配線を使用しています。大型バイクに限ってですが、最近、「CAN(Controller Area Network)バス通信」というシステムが搭載されるようになりました。以前は非常に長い配線を大量に使っていたため、重量も然ることながら、コストも高かったのですが、CANシステムにすることで、配線を大幅に削減することができました。商品を作る我々の立場としては、なるべく配線の数を少なくしたい、というのが現状です。
◆ CANとは?
CANとは、自動車をはじめ、工場の自動化(FA)、産業機器など、多岐にわたる分野で利用されているシリアル通信プロトコルで、約30年前にドイツのボッシュ社によって開発されました。現在では皆さんが乗る自動車のほとんどにCANシステムが搭載されており、エンジン制御やブレーキ制御等のスタビリティコントロールを行っています。
なぜCANの開発が求められるようになったのかというと、自動車の高機能・高性能化に伴い、車両内の電子制御ユニット(ECU:Electronic Control Unit)が激増したためです。最初はエンジンコントロールユニットひとつだけだったのがどんどん増加し、最近ではパワーウィンドウの安全装置やブレーキスタビリティコントロールなど、100以上のECUを搭載するようになっています。それらひとつひとつを配線してつなげると複雑化し、重量や部品点数も増え、製造コストが跳ね上がってしまいます。さらに配線スペースの問題も引き起こします。その解決策が、少ない配線でも高速で確実な通信ができるCANだったのです。
◆ CANバス通信とは?
CANバス通信の「バス」とは、路線バスに由来し、バスの路線上にある停留所のように、各ECUを1本の線でつなぐ接続方式です。従来方式の配線では、ECUとECUを複数の配線で接続し、それを20、30も複雑に組み合わせていましたが、その複数の部品間配線を1本の通信線にまとめて各ECUで共有しよう、というものです。
CANバス通信にすることで配線本数は減るため、軽量化され、コストの問題は克服できます。さらに、1本のライン上で故障点検や整備ができるようになるため、整備性も向上します。デジタル通信ということで、耐ノイズ性や耐浸水性を心配される方も多いと思いますが、ボッシュ社が開発したCANバス通信はアナログ並に強いシステムです。また、後ほど詳しく説明しますが、ダイアグ通信による故障診断を容易にし、測定/キャリブレーションを迅速にします。
このほかCANシステムのメリットとして、車体重量の軽量化のみならず、配線スペースの確保が容易になる点が挙げられます。オートバイは非常にコンパクトに作る必要があり、配線ひとつ通すスペースを残すことも問題になります。コンピュータがまだ搭載されていない従来のオートバイの時は、設計後に電源線を通せばよかったのですが、コンピュータの数が激増したため、設計前に電源線を通すためのスペースを確保しておく必要性が生まれました。CANシステムになったことで、電源線を通すスペース確保が楽になったのです。
また、配線本数が減ることで物理的な故障も減少しました。オートバイの場合、首振りで、ハンドルを切るたびにハーネスが動かされます。すると、ハーネスが引っ張られて切れるといった物理的な故障のリスクが、配線数が多いほど高まります。それがCANになることで、線が1本切れるだけですから、故障を発見し易くなりました。また以前は故障診断時、ECUを個別に検査する必要がありましたが、CANによってネットワーク全体の故障診断や処理を一箇所でできるようになりました。
◆ 通信の変革 複数線から単線へ
初めてCANが使用されたオートバイが、2004年に発表されたBMW社の「R1200GS」です。ただし、BMW社の広告では「従来モデル比で30kgもの車体軽量化に大きく貢献」と謳っていますが、実際に当時それだけの効果があったかと言えば、疑問です。基本的には、当時はメーターとエンジンコントロールシステムにCANバス通信を使用しただけで、他にはあまり多くのコンピュータを搭載していない車両でしたから、現在の車両ほど軽量化の効果はなかったと考えられます。おそらく現在の高機能化した車両であれば、30kg近い配線本数の削減に結びついていると思います。とはいえ、人間で言う、神経系統に似た電気配線システムをCANバス通信にした意味では画期的な商品でした。
◆ CANの種類
CANの規格には、主に「低速CAN」(毎秒125キロビットまで)と「高速CAN」(毎秒1メガビットまで)の2種類が使われます。両規格ともノイズの影響を受けにくくするために2本の通信線を使用しています。基本的にCANバス通信は、この2本の通信線の上にECUがつながっていれば成り立つというシステムです。CANの通信線の配線方法は、高速CANと低速CANで異なります。低速CANの方が、やや複雑な配線方法となります。
また、アメリカ自動車技術会(SAE:Society of Automotive Engineers)では、通信速度で「クラスA」から「クラスC」まで分類しています。クラスAは最大通信速度毎秒10キロビットで、用途はライト類やパワーウィンドウ、ドアロック等。クラスBは最大通信速度毎秒125キロビット(低速CAN)で、用途はメーターやオートエアコン等。クラスCは最大通信速度毎秒1メガビット(高速CAN)で、エンジンやトランスミッション、ブレーキの制御等のリアルタイム制御系に用いられます。
このようにCANは高速化してきました。例えば、自動車で横滑りした時、エンジン出力を下げる制御は高速に行われる必要があるためです。ただし、CANの通信速度には上限があるため、高速で追いつかない場合は、ECU同士を直接つなげたものを併用しながら組むことが実際には行われます。ですから、CANだけで成り立つわけではありません。
◆ 故障診断通信
先程も説明しましたように、CANバス通信によって、迅速に車両の不具合を発見できるようになりました。例えば、不具合が出た場合にメーターへエラーコーションを出すことが非常に容易にできます。我々が車両開発をする時も、エラーが手に取るようにわかるため、開発も楽になりました。さらに開発中は、従来使われていたような9ピンのコネクタ等で簡易的なハーネスを作って試験を行いますが、開発中の装備とも簡単に接続できます。
皆さんにも身近な故障診断通信の事例を挙げると、自動車にダイアグ(Diagnostic:診断)通信を接続して故障診断を行えます。皆さんの自動車のダッシュボードの下にも、最近は「OBD-IIコネクタ」と呼ばれる専用コネクタを見つけることができるはずです。ここにCANバスに通じる端子があります。数千円で市販されているスキャンツールをこの端子に挿すだけで、ECUにアクセスし、燃料残量や平均速度といった情報を得られます。最近はもうこの部分まで無線化が進んでいます。
◆ 測定/キャリブレーション
現在の電子化された自動車や生産機械等では、制御全体を最適化(キャリブレーション)する工程が必要になります。その際にECUへアクセスするためのプロトコルを「測定/キャリブレーションプロトコル」と言います。最近はCAN以外のシリアル通信プロトコルも自動車に搭載されるようになりましたが、「ASAM(Association for Standardisation of Automation and Measuring Systems)」という規格を使えば、異なるネットワークにも対応でき、簡単に色々なことができます。
◆ 通信プロトコルの種類
車載ネットワークには、CAN(最大通信速度毎秒1メガビット)のほかにも、「LIN」(最大通信速度毎秒20キロビット)、「FlexRay」(最大通信速度毎秒10メガビット)、「MOST」(最大通信速度毎秒24.8メガビット、毎秒50メガビット/毎秒150メガビットの規格もあり)などの通信プロトコルがあります。現在の車載ネットワークはCANが一般的ですが、これから高速化が必要な自動運転化でFlexRayに移行し、さらに車のマルチメディア化によってMOSTへ移行するでしょう。LINはCANと同じくバス停のように1本のワイヤーハーネス上にECUを並べるバス型ですが、FlexRayは複数のECUを放射状に連結できる「スター型」等の接続方式にも対応可能なため、より高速な通信が可能です。
◆ 今後の展開は、費用対効果次第!
では今後、ハーネスは無くなるか?と言えば、それは費用対効果次第でしょう。最近は、小型バイクもインジェクション(電子制御式燃料噴射システム)となり、ABSの義務化が世界標準となりましたが、小型バイクの場合、せいぜいABSを単独で動かしてエンジンコントロールとメーターを接続するだけですから、CANにする必要はありません。それに、もともと配線本数も少ないです。そのような小型バイクを、ヤマハは年間約450万台生産していますが、すべて海外生産でハーネスも海外調達です。一方、大型のバイクだけは国内生産ですが、最新鋭のバイクには5軸ジャイロ等を搭載しているため、どうしてもCAN通信を採用しなければ成り立たないのが現状です。これから複数の制御の高度化と軽量化を達成するために、CANを含めた高速通信へますます移行していくでしょう。そのため国内では従来品の移動体用のハーネスは無くなっていくと思います。
これから電気自動車が普及すれば、大電流への対応としてラインも太くなるため重量が増大します。そのため、銅製品よりも軽く、高強度な低コストのアルミワイヤーハーネスが今後検討されるかもしれません。
船舶については、重量をそれほど心配する必要はありませんが、最近はさまざまなことが自動化されたことに伴い、コンピュータ同士を接続する必要性が増えました。船舶は大型のため線が長くなる分、コストダウン効果が大きく期待できるため、CANバス通信の採用例は増えていくでしょう。また、船舶は重量的に余裕があるため、光通信の可能性もあるかもしれません。光通信は、光を電気に変換する様々な付属品が必要なため、バイクのように軽量化をねらう小型車両には難ですが、船舶であれば採用されていく可能性があります。
一番の問題は、無線化ですね。実際に皆さんがお使いのキーレスエントリーシステムも、無線化した事例と考えてよいと思います。そのようなものが現実的に今後、どんどん増えていくでしょう。例えば、ロードレース用自転車のディレイラー(変速装置)は、以前は鉄ワイヤーで機械的に動かしていたものが、数年前にシマノ社がCANを用いて電動ディレイラーを開発・販売し、昨年はスラム社がCANを止めてしまいました。ついにディレイラーのコントロールも無線化したのです。これでコントロール系統の線は、ブレーキ以外は完全に無くなってしまいました。そのような形でワイヤーハーネスは、高付加価値品に限られるかもしれませんが、将来的には無くなっていく傾向にあります。それは移動体に限らず、産業機器等に関してもその可能性が高いでしょう。
◆ モーターサイクルにおける開発評価
当社のモーターサイクル開発におけるハーネスの評価についてもご紹介します。電波暗室TEMセル試験では、想定される電波を出して影響を受けないかを電波暗室内で試験します。シャワーテストでは、水をかけて、漏電による不具合が発生しないかをテストします。
首振り耐久は、オートバイの場合はハンドル部分が回るため、何万回もハンドルを動かし、ハーネスの不具合が発生しないか、テストします。ハーネスは大量の線をポリ塩化ビニルのテープで束ねてできているため、曲げられるたびに、内側の線は曲げられ外側の線は引っ張られるところが常に問題となるのです。
実走行耐久評価では、走行時の振動によって柔らかな線が内部で破綻しないかをテストします。ワイヤーハーネスは金属ですので、やはり振動には非常に弱いのです。もちろん、機能が損なわれていないかの機能テストも行います。
組込性評価は、どこに線を通すかが重要で、無理やり通してたわんでしまうと、そこに水が溜まってしまいます。ですから、高いところから低いところへ配線するように気をつけて、組み込み後の状態を評価します。また、いろいろな外付けのものを取りつけた時に不具合が起きないかもテストします。
「検車会・わいがや」では、オートバイを前に、ワイヤーハーネスも含めて、いろいろな部分について想像力を働かせ、「どんな問題が将来起き得るか?」等と想像しながら会議を行っています。
◆ ワイヤーハーネスの規格・標準
最後に、ワイヤーハーネスにも現在、様々な国際規格があることを紹介して、私のお話を終わります。
講師と参加者による議論
(参加者) 結局、これからハーネスが無くなる変化に対応していかなければ、ハーネス業は生き残れない、という結論ですか?
(松本) その可能性があるということです。少なくとも、先程もお話したように、自転車のコントロールワイヤーが無くなり、次に電動化した信号線が無くなり、現在は無線化したという事例があります。高付加価値な自転車の事例ですが、今後無線チップの低価格化が進めば、いろいろなものに応用され、ワイヤー業が無くなる可能性はあると思います。
(参加者) 本日は移動体に関するお話でしたが、産業機器も同様と考えてよいですか?
(松本) 故障判断は、CANバス通信のように、シンプルな通信経路の方が容易なため、高い信頼性が求められる産業機器も、シンプルなラインになる可能性があります。ただし、産業機器は高速化しており、CANには通信の上限があるために、ECU同士を接続する必要がある部分は、ハーネスが無くならない可能性はあります。逆に、低速でも問題ない部品はCANバス通信に置換されていくでしょう。
(参加者) 現実的にハーネスの需要は増えている傾向もあるのですが。
(松本) 現実的には機能がどんどん増えているので、仰る通り、配線の数は増えています。
(参加者) 高級車種ほど、信頼性の面でも、ハーネスの需要があります。
(松本) 問題は、日本国内では高付加価値品しか生産しなくなっていることです。ヤマハも現在450万台を生産していますが、このうち国内生産は数万台だけで、それ以外の9割以上が海外メーカーによる生産です。ワイヤーハーネスの調達先も海外ですので、従来のお仕事は海外に取られていきます。数は少なくはなりましたが、残った高付加価値なハーネスは国内で生産していますが、さらに新規格が今後出、その変化に追いつかなければ、国内では仕事が無くなる可能性があります。
(井ノ上) CANバス通信という新技術が入った影響でハーネスは減りますが、仰る通り、高機能化に伴い、ハーネスは増えています。そこにさらに高速化という追加の要求が入ってきます。その要求にどう応えるか。
また、光ファイバーは光を全反射させるため損失無しで遠く離れた場所へ光の信号を伝えることが可能ですが、センサの電気信号を光に変換してから送った先で光を電気に戻してECUに入れる必要があります。そのコストと重量に現在のところは優位性がないため、しばらくは光通信にならないだろうと松本先生は仰っています。しかし、数年後に国際基準ができ、世界中で同じものを一気に量産できるようになれば、コストは下がるでしょう。救いは、それまでにあと何年かあり、対策の立てようがあることです。
もうひとつ、ぜひ質問いただきたいのが信頼性です。無線は外部からの影響を受けやすい。命を守るようなコントロールを無線に任せていいのでしょうか?そこは線でしょう?
(松本) そこは線でしょう、というのは確かにあるかもしれませんが、混信しないようにそれぞれペアリングを行っています。今はWi-FiやBluetooth等の技術がありますが、信頼性向上のための独自規格を開発している方たちもいます。そのうち何かが国際基準として採用されれば、それに乗り遅れないように自分たちも勉強する、その繰り返しではないでしょうか。
(参加者) Wi-Fi等の無線ではノイズが入ることがありますが、どのような対策を取っていますか?
(松本) ノイズの問題は技術の進歩で解消できます。例えば、昔はマイクとスピーカーを近くに置くと、「キ~ン」と鳴っていましたが(ハウジング)、今は起こらないですね。それはスピーカーから出る音とマイクに入る音を計測し、その信号を見比べながら、ソフト上で管理しているためです。
(参加者) 将来的にはセンサにCPUが入り全体の要素を動かすようになる可能性が高い、と解釈してよろしいですか?
(松本) 当社の最上級1,000ccバイクの売りのひとつは「転ばない(転びにくい)バイク」です。その中核を担うのが、姿勢制御を行う5軸ジャイロセンサで、当社の特徴はジャイロにCPUを載せ、そこで処理をしてエンジンコントロールを行うことです。今ではCPUが付いていないセンサを探すのが難しいところまで、すでに来ていると思います。
(参加者) CANバスは、USBのLANケーブルというイメージですが、コネクタの加工技術等の国際的な規格などは、既に決まっていますか?
(松本) 「自動車には自動車用のコネクタや線を使用してください」くらいはありますが、電子信号が伝われば基本的には何でもよく、汎用品で十分成り立つシステムです。ですから、極端な話、USBケーブルを使ってもよいですし、私たちのプリテストでも9ピンコネクタを使っています。
(井ノ上) 国内と海外の企業によって商慣習が異なると聞いています。日本企業の場合は、「A社のBを使いなさい」と型番が指定されるのに対し、欧米の企業の場合は「JIS規格の何番」と指定されるだけで、同じJIS規格の部品であれば何を使ってもよいらしいですね。その辺りの商慣習は今後どうなっていくでしょうか。
(松本) やはり我々メーカーは、「A社のB」でしかテストをしたことがないので、「A社のB」と商品名に近いものを指定するでしょうね。我々メーカーがハーネスメーカーさんに直接お願いする場合もあれば、基盤メーカーさん経由でお願いする場合もありますが、後者の場合、直接お話する機会もないので、融通できなくなる面もあります。また、先ほどの「OBD-IIコネクタが規格化されている」という話も、四輪車は割と統一されていますが、二輪車の場合は「ピンの位置が微妙に違う」ことが多々あります。
(参加者) ハーネス自体は無くなることはないけれども、今後の技術革新でさらに本数が減らされていく、という認識でよろしいですか?
(松本) 同じ機能であれば減ります。人間が「もうこれ以上、便利にならなくてよい」となれば、減っていく可能性がありますし、「もっと高機能な車をつくってほしい」となれば、増える可能性があります。そのどちらに動くかです。ただ、技術革新が進むほど、メーカー側の気持ちとしては当然、コストダウンや軽量化、シンプルさ等を求めて減らしたいです。ただ、「機能をどんどん増やしてほしい」というユーザーさんからの要望があるため、今のところは増えています。
(参加者) ハーネス加工メーカーは今、最初に何に取り組む必要があると思いますか?
(松本) とりあえず、まずは「かじる」ことが重要だと思います。次にどんな技術が登場するかをWeb等でよく勉強していれば、次にどんな技術が必要なのかわかってきますから、先回りして事業を展開できるのではないでしょうか。
(参加者) 軽量化や信号量の観点から見ると、光ファイバーにした方がよいですか?
(松本) そうですね。ただ、我々の車両の中では、すぐには光通信にならないと思います。ただ、据え置きのFA産業機器であれば、光通信になる可能性が高いでしょう。
(井ノ上) 発注者側は、一体どんなことを考えて、どんな評価をしているのでしょうか。松本先生のご講演の最後に「わいがや会議」がありましたが、どんな議論をされているか、もう少し教えていただけないでしょうか。例えば、防水について。
(松本) 水は、防水すれば防水するほど、実は溜まるのです。水を抜け易くするためには、どうも水は入り易い方がよい。そういうことも、ひとつひとつ技術です。例えば「これは水が入っちゃうよね。でも必ず抜けるようにしないといけない」ということを話し合ったり、先程もお話したように、ワイヤーがたるむと水が溜まるので、「たるんでいる」と指摘してもらったりするのが、「わいがや」です。当然、水が入ってくれば一緒にホコリや砂も入り、故障の原因になるので、本当は水が入らない方がよいに決まっています。それをハーネスメーカーさん側で提案してくれるとよいかもしれないですね。ただし、「必ず水が入らない」「どの程度の耐水性がある」と証明しなければ誰も採用しません。県や国の試験研究機関でエビデンスをつくり、メーカーに提案するのも、ひとつの方法だと思います。
(参加者) 発注者側の企業は、ハーネス加工メーカーからのフィードバックは望んでいるのでしょうか?
(松本) 「コストダウン会」は当然行います。社内の管理職のほかに、メーカーさんにも参加いただきますが、お呼びするのは一次協力企業さんだけです。そのような場に参加させてもらえる会社になりましょう、ということだと思います。
(井ノ上) ある企業は発注が来ても、「この図面では安くできない。この図面をこう変えさせてくれたら、当社ではいくらコストダウンできます」と「逆提案」をしているそうです。最初は二次、三次下請けで、なかなか一番上の発注企業と会えなかったそうですが、逆提案を繰り返していくうちに発注企業の技術展示会に呼んでもらえて、つながりができたそうです。逆提案型で参入していく企業はたくさんあります。
(参加者) 一次、二次下請けを飛ばしてしまうので、やりづらいと思うのですが。
(松本) 当社でも、面識はあるものの、取引のない企業と一緒に社内展示会を行う機会はあります。一般の展示会などに積極的に参加しメーカーさんとの交流を図ることも、やはり必要ではないでしょうか。
(井ノ上) 展示会も、「図面があれば作れます」だけでは、出展させてもらえませんから、「当社はこういうものをつくれます」と、何かしらのサンプルを作って持ち込むことが必要ですね。
(松本) 実は、ヤマハのバイクの部品を専門に作っていたある企業さんの場合、海外生産にシフトした影響で、仕事がどんどん減ってしまいました。そこで、その企業さんは自動車の部品を作ろうと考えて自分たちで作れるものを探して、頼まれなくても勝手に型を起こして作り、T社に提案して採用されたそうです。機械加工と溶接がメインの会社が、溶接組み立て部品を後加工しなくとも車に取り付けられる精度を出せる技術を独学で身につけ、採用された事例です。そこまで努力されています。
(参加者) ヤマハさんは、大型のバイク以外で、メイドインジャパンの取り組みを行っていらっしゃいますか?
(松本) コストが見合わないものはどうしても海外へシフトしますが、国内生産できるものはなるべく国内生産するのが基本です。それは雇用を守るためです。当社では創業以来、社訓に「事業活動を通じた国家社会への貢献」を謳い、雇用と納税を守ることが事業の根本であると教えられてきました。
日本語では「メーカー」と言いますが、我々は「コンプリートメーカー(組み立てメーカー)」であり、部品は部品メーカーの皆さんから調達します。部品を作る皆さんが、技術力や信頼性、供給能力等で高いレベルになければ、我々も存続することができませんし、日本も存続できないでしょう。
(井ノ上) 今日お伝えしたかったことの1点目は、技術は日進月歩で、新しい技術が登場するたびに対応しなければ取り残されてしまう、ハーネスにもその動きがあるということ。2点目は、信頼性を中心にメタルのハーネスは当面残る。その間に、今後どのように技術が変わっていくかを見越して、現在の業務と並行してご準備いただきたいということ。それが私どもの願いです。開発には当然お金がかかりますので、必要があれば、県や国の補助金もご活用ください。私どもも一生懸命応援させていただきます。これから様々な変化がある中、力を合わせ、東北地域を盛り上げていきましょう。
参加者インタビュー
◆ 技術革新に備える必要性を再認識
/株式会社岩本電機 代表取締役社長 岩本 崇司 さん
産総研の井ノ上さんからお声がけいただき、ハーネスをテーマにしたEBISワークショップを開催いただきましたが、実際にやってみて本当に良かったです。当社はワイヤーハーネスの加工メーカーですので、これからお客様の需要がCANバス通信に移行した時、しっかり対応できるようにしておくことが今から必要であるとの気付きを得ました。さらに、お客様から依頼された時のみならず、「逆提案」できるようになるため、まずは勉強しなければいけない、そのキックオフになったと思います。最初は「ハーネスが無くなる」というネガティブな話でしたが、では今から何をしなければいけないのか、改めて気づかされたワークでした。
◆ CANバス通信や新規格に対応できるハーネス加工技術を学びたい
/有限会社幸電子 工場長 盛田 秀昭 さん
当社もハーネス加工の会社で、「ハーネスの未来」というテーマに興味を惹かれて参加しました。自動車用ハーネスは、何本も線を組み込んで束ねていく「組みハーネス」という非常に難しい技術で、専門の業界があるほどですが、それが簡略化されるお話は大変興味深かったです。また、今後ハーネスが減るとはいえ、メインハーネス以外は今後も増えていく要素が残っている点も、興味深いです。新しいCANバスのハーネスもある程度需要が出てくると思いますし、その製作技術はUSBケーブルやLANケーブルと同じ規格になっていくとすれば、それに伴う加工の治具や規格に対する技術も今後学ぶ必要があると考えています。
◆ 安全を総合的に実現する材料研究につなげたい
/八戸工業大学大学院工学研究科 教授 信山 克義 さん
私の専門は電子・電気材料工学です。ハーネスの中にはメタルがあり、その周囲には絶縁体がありますので、絶縁体に今後どのようなことが求められるかを勉強するために参加しました。電気的なことだけでなく、機械的なことや通信高速化等も含めて、安全に長期間使える絶縁体の開発が今後求められると感じました。今後は無線化が進んでいくと思いますが、ハーネスが必要な領域は残るでしょうし、大学でも「安全に長く使う」ことを総合的に考えて絶縁体の研究を行っていきたいと考えています。
コラボレーション
おすすめ記事
![]() |
【特集】宮城の研究施設 一般公開特集 |
![]() |
【特集】仙台市総合計画審議会 仙台の10年をつくる |
【社会】社会って、そもそもなんだろう?

青井真さん(防災科学技術研究所)に聞く:<東日本大震災から10年>東北地方太平洋沖地震が起きて、地震研究はどう変わった? 2021.11.11 【大草 芳江|社会って、そもそもなんだろう?|科学って、そもそもなんだろう?|防災科学技術研究所】

前田拓人さん(弘前大学)に聞く:<東日本大震災から10年>もし東北地方太平洋沖地震が起きていなければ、地震研究はどうなっていた? 2021.10.08 【大草 芳江|弘前大学|社会って、そもそもなんだろう?|科学って、そもそもなんだろう?】

日野亮太さん(東北大学)に聞く:<東日本大震災から10年>もし東北地方太平洋沖地震が起きていなければ、地震研究はどうなっていた? 2021.10.02 【大草 芳江|東北大学|社会って、そもそもなんだろう?|科学って、そもそもなんだろう?】
同じ取材先の記事
◆ 産業技術総合研究所東北センター

2050年カーボンニュートラル実現にむけた技術革新とは?<産総研化学プロセス研究部門インタビュー> 2021.08.31 【大草 芳江|産業技術総合研究所東北センター|社会って、そもそもなんだろう?|科学って、そもそもなんだろう?】

「技術を社会へ橋渡し」する産総研東北センターの産学官連携活動とは?<産総研東北センター上席イノベーションコーディネータの南條弘さんに聞く> 2021.08.31 【大草 芳江|産業技術総合研究所東北センター|社会って、そもそもなんだろう?】

産総研東北センターが新たに掲げた看板研究テーマ「資源循環技術」とは?(2/2)<産総研 資源循環利用技術研究 ラボ長の佐々木毅さんに聞く> 2021.05.25 【大草 芳江|産業技術総合研究所東北センター|科学って、そもそもなんだろう?】

産総研東北センターが新たに掲げた看板研究テーマ「資源循環技術」とは?(1/2)<産総研東北センター所長の伊藤日出男さんに聞く> 2021.05.25 【大草 芳江|産業技術総合研究所東北センター|科学って、そもそもなんだろう?】
社会って、そもそもなんだろう?
最新5件
カテゴリ
取材先一覧
■ 幼・小・中学校
■ 高校
- ・仙台一高 (15)
- ・仙台二華 (14)
- ・仙台二高 (12)
- ・仙台城南高校 (5)
- ・仙台城南高等学校 (0)
- ・仙台高専 (4)
- ・宮城一高 (4)
- ・宮城県高等学校理科研究会 (2)
- ・岩ケ崎高 (1)
- ・東北工業大学高校 (0)
■ 大学
■ 国・独立行政法人
- ・内閣府 (1)
- ・宇宙航空研究開発機構 (5)
- ・文部科学省 (0)
- ・東北経済産業局 (17)
- ・水産総合研究センター東北区水産研究所 (1)
- ・理化学研究所 (3)
- ・産業技術総合研究所東北センター (36)
- ・科学技術振興機構 (1)
- ・防災科学技術研究所 (1)
- ・高エネルギー加速器研究機構 (1)
■ 自治体
- ・仙台市 (8)
- ・仙台市博物館 (4)
- ・仙台市天文台 (12)
- ・仙台市教育委員会 (13)
- ・仙台市産業振興事業団 (1)
- ・仙台市科学館 (8)
- ・仙台文学館 (2)
- ・仙台管区気象台 (2)
- ・塩釜市 (3)
- ・宮城県 (8)
- ・宮城県古川農業試験場 (2)
- ・宮城県教育委員会 (1)
- ・宮城県農業・園芸総合研究所 (1)
- ・気仙沼市 (1)
- ・登米市 (1)
■ 一般企業・団体
- ・DIC株式会社 (2)
- ・K sound design (1)
- ・KDDI (2)
- ・natural science (1)
- ・せんだい・みやぎNPOセンター (2)
- ・てとてと (1)
- ・ひのき進学教室 (11)
- ・みやぎ工業会 (8)
- ・みやぎ工業会会長 (0)
- ・みやぎ産業振興機構 (3)
- ・アスター (1)
- ・インスペック (1)
- ・エツキ (1)
- ・ソニー (3)
- ・ソニー教育財団 (1)
- ・ソフトバンク (1)
- ・ティ・ディ・シー (1)
- ・デュナミス (1)
- ・ドットジェイピー (1)
- ・ナノテム (1)
- ・ハリウコミュニケーションズ (3)
- ・ハード工業有限会社 (1)
- ・フジイコーポレーション (1)
- ・プレファクト株式会社 (1)
- ・ヤマダフーズ (1)
- ・全国学習塾協会 (3)
- ・公益社団法人セーブ・ザ・チルドレン・ジャパン (1)
- ・勝山酒造部 (1)
- ・及源鋳造株式会社 (1)
- ・大武・ルート工業 (1)
- ・太白少年少女発明クラブ (1)
- ・宮城の新聞 (0)
- ・宮城県中小企業家同友会 (1)
- ・宮城県産業人クラブ (0)
- ・宮城県職業能力開発協会 (1)
- ・宮城県酒造組合 (2)
- ・工藤電機 (2)
- ・平孝酒造 (1)
- ・応用物理学会 (2)
- ・新東総業株式会社 (1)
- ・日刊工業新聞社 (7)
- ・日本アンドロイドの会 (1)
- ・日本技術士会 (2)
- ・日本私立大学団体連合会 (1)
- ・日本農芸化学会東北支部 (1)
- ・日本IBM (3)
- ・日東イシダ (1)
- ・有限会社 柏崎青果 (1)
- ・東京エレクトロン宮城 (1)
- ・東北ニュービジネス協議会 (1)
- ・東北活性化研究センター (3)
- ・東北経済連合会 (1)
- ・東北電力 (2)
- ・東北電子産業株式会社 (1)
- ・東栄科学産業 (1)
- ・林精器製造 (1)
- ・株式会社三栄機械 (1)
- ・株式会社悠心 (1)
- ・河北新報 (1)
- ・神田産業株式会社 (1)
- ・秋田化学工業 (1)
- ・笹氣出版印刷 (1)
- ・米鶴酒造 (1)
- ・萩野酒造 (1)
- ・農芸化学会 (1)
- ・遠藤工業 (1)
- ・鈴木製作所 (1)
- ・阿部蒲鉾 (1)
- ・阿部蒲鉾店 (1)
- ・鳴子の米プロジェクト (1)
- ・NECトーキン (1)
特別企画 「宮城の塾」
![]() |
学習塾から見る 宮城の教育の「今」 塾選びに一役 |

![]() |
【科学って、そもそもなんだろう?】 若手研究者座談会「地震学×情報科学の融合で得られたもの」 2024.09.16 |
![]() |
【科学って、そもそもなんだろう?】 地震の発生予測に挑む(京大防災研の西村卓也さん・京大名誉教授の平原和朗さんに聞く) 2023.01.26 |
![]() |
【社会って、そもそもなんだろう?】 【同窓生に聞く#01】中鉢良治さん(元ソニー社長、産総研最高顧問)がリアルに感じていることって、何ですか? 2022.10.27 |
![]() |
【科学って、そもそもなんだろう?】 地震学×情報科学の融合で、目指すは天気予報の地震版 2022.04.13 |
![]() |
【社会って、そもそもなんだろう?】 「仙台の地形と水との関わり」~地形から見る仙台の過去・現在・未来~ 2022.03.02 |
![]() |
【科学って、そもそもなんだろう?】 青井真さん(防災科学技術研究所)に聞く:<東日本大震災から10年>東北地方太平洋沖地震が起きて、地震研究はどう変わった? 2021.11.11 |
記者ブログ
![]() |
ひとり新聞社「宮城の新聞」の大草よしえが衆院選に立候補 2021.10.19 |
![]() |
最近の活動は「Twitter」に移行しました 2019.11.01 |
![]() |
【追記】テレビ朝日「モーニングバード」スタジオ生出演&iCAN'15世界大会(アラスカ)世界第1位! 2015.06.19 |
![]() |
2014年の振り返りと、2015年の抱負 2015.01.05 |
![]() |
平成25年度を振り返りました・・・。 2014.04.02 |
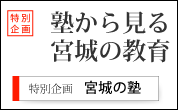
![]() |
中野塾(泉中央・北高森) |
![]() |
ひのき進学教室(泉中央・長命ヶ丘・八幡教室・上杉教室) |
![]() |
夢学館(東照宮・福室) |
![]() |
早稲田育英ゼミナール(泉中央) |
![]() |
ソーメック個別学習院(若林区、太白区、泉区に6教室) |
![]() |
明和塾(北山・八木山) |
![]() |
JUKU ペガサス仙台南光台教室(南光台南) |
アクセスランキング
- 【宮城の塾】 宮城の塾 仙台市を中心とした学習塾・幼児教室・進学塾の特集
- 世界中の研究者が憧れる研究拠点へ/東北大学WPI-AIMR本館竣工記念式典/科学って、そもそもなんだろう?
- [vol.1] 第1回宮城の日本酒を楽しむ会/社会って、そもそもなんだろう?
- 「仙台の地形と水との関わり」~地形から見る仙台の過去・現在・未来~/社会って、そもそもなんだろう?
- 宮城県仙台第一高等学校/教育って、そもそもなんだろう?
- 【宮城の塾】 ひのき進学教室(泉中央本部教室・八幡町教室・上杉教室・五橋教室・長町教室・愛子教室・吉成教室・大和町教室、他)
- 地震の発生予測に挑む(京大防災研の西村卓也さん・京大名誉教授の平原和朗さんに聞く)/科学って、そもそもなんだろう?
- 【宮城の塾】 JUKU ペガサス仙台南光台教室
- 【宮城の塾】 質問できます!/宮城の塾|宮城の新聞
- 【宮城の塾】 明和塾(北山教室・八木山教室)