取材・写真・文/大草芳江
2018年05月01日公開
ものの見方を変えて、
「できない」を「できる」に変える、
理に適ったものづくり。
株式会社ナノテム(新潟県長岡市)
代表取締役 髙田 篤 Atsushi Takada
公益財団法人東北活性化研究センター『"キラリ"東北・新潟のオンリーワン企業』Collaboration連載企画 (Vol.20)
新潟県長岡市に本社を構える株式会社ナノテム(1998年設立、従業員18名、資本金1億2,550万円)は、セラミックス焼結技術をコア技術とし、革新的な真空吸着プレート(真空チャック)や研削・研磨用特殊砥石を開発・製造している、国立大学発第一号のベンチャー企業である。独自のセラミックス焼結技術で、多孔質セラミックスの気孔を自在に制御することにより、様々な商品を開発。セラミックスから水や空気を自在に出し入れすることにより多様な機能を実現した。微細な気孔から空気を吸出し、セラミックス表面に研磨物を貼り付けて作業ができる真空チャックを実現。顧客の要望に合わせた仕様で最大2.5m角まで対応できる。半導体や液晶・有機ELといった分野から注目され、国内外の製造現場で導入されている。また、多孔質セラミックスによるダイヤモンド砥石を開発。被加工物の材質に合わせて任意に設計が可能。セラミックス素材をベースとした、ダイシングブレード、研削盤等の製造も手がけている。2009年「アドバンスト ディスプレイ オブ ザイヤー 」部品材料部門優秀賞、2010年 科学技術分野の文部科学大臣表彰、2012年「第46回グッドカンパニー大賞」新技術事業化推進賞、2014年 新潟県技術賞、2016年 経済産業省 中小企業庁「はばたく中小企業・小規模事業者300社」等、数々の賞や認定を受けている。そんなオンリーワン企業であるナノテムがオンリーワンたる所以を探るべく、代表取締役の髙田篤さんに話を聞いた。
オンリーワン企業になるまでの軌跡
― はじめに、貴社がオンリーワン企業と言われる所以と、それに至るまでの軌跡を教えてください。
◆ ダイヤモンド工具で起業するも、参入の難しさを痛感
オンリーワンかどうかはわかりませんが、確かに"オンリーワンっぽい"んですよ。やっていることは"変"と言えば変ですね。人がやらないことをやっています。それは、やっても儲からないからかもしれませんが、うちは小さな会社だからやれるのです。会社の規模が大きければ、おそらく、どこも手を出さないでしょう。
実は最初、ダイヤモンドの工具(多孔質セラミックスによるダイヤモンド砥石)を"攻め"たくて、約20年前に起業しました。ところが砥石は、我々のような小さな企業が参入するのが非常に難しい業界であることを、起業して1年目に痛感しました。
― なぜ参入が難しいと感じたのですか?
私が思うに、工具業界の商売の主流が、砥石のサンプルを無償提供する形態であることが、資本力に乏しいベンチャー企業が参入しづらい要因になっていると思います。具体的には、工具をつくるのに約1ヶ月、それをお客さんがテストして評価するまでに約1ヶ月、長い場合は約4ヶ月もかかります。テスト後、お客さんに「この工具、よく切れるでしょう?」と聞くと、「おお、よく切れるね」の"次"が必ずあって、「でもね」から入り「もっと寿命が長くならないかな」と次の課題を言われるのです。「わかりました」と次の課題についても無償提供のサンプルをまた1ヶ月かけて準備し、3ヶ月かけてテストしてもらう時点で、もう半年を超えていますよね。また次も、「いい感じにできたね」の次にやっぱり「でもね」が入り、「もっとピカピカにできないかな」と、要はお客さんの要求レベルが課題をクリアするたびにどんどん上がるのです。やっと3つ目の課題もクリアしたと思ったら、今度は材料が変わって、もう一回振り出しに戻るという、もっと恐ろしい話だってありました。
はじめは「よいものをつくれば買ってくれる」と思っていましたが、よいものをつくったからと言って、必ずしも買うところまではいかないことを痛感しました。さらに、よいものだからといって、誰も人には言わないのです。皆が加工できるようになったら加工屋さんは困るので、逆に内緒ですよ。すると売上もそんなに上がらないですし、時間もお金もかかるし、これは厳しいなぁと。ものづくり以外の要因で、ものづくり系のベンチャー企業は淘汰される仕組みになっていると気付きました。そこで実は工具はメイン事業にしない方針に、2年目から変えました。たまたま私は運良く回っただけで、"それ"がなければ回らなかっただろうと思います。
◆ 自分たちが必要だから開発した「真空チャック」が転機に
― それからどのようにして「運よく回った」のですか?
ものを削る時、何かで固定する必要がありますよね。一般的な固定方法はクランプという金具で抑えて固定します。ただ、クランプで抑えた部分は削れないため、クランプの位置をずらしながら何度か削る必要があり、それによって段差ができてしまうので、本当は一度に削れる方がよいのです。あるいは、クランプを使わず磁石で固定する「マグネットチャック」という方法もありますが、鉄にしか使えないので、例えばガラスやプラスチック、セラミックスなどの非磁性体には使えません。
実際に、自分たちも開発した工具を評価する際に固定する治具が必要だったので、我々は、真空を引いてワーク(加工するもの)を吸着する「真空チャック」という手法をずっと使っています。はじめは市販の真空チャックを使っていたのですが、問題点が幾つかありました。従来型は、アルミニウムやステンレスの吸着面に溝や穴を設けてワークを吸着する仕組みなので、すぐ目が詰まって真空が効かなくなりますし、真空を引くと溝や穴の部分がへこみ、真空を外すとその部分が出っ張るので、たわみができ、高精度な加工ができませんでした。もうひとつの問題は、ワークのサイズは吸着盤と同じでないと吸着しないことです。吸着盤の溝や穴をすべてふさがないと、空気が漏れて吸着する力が生まれません。そうなるのは当たり前の話ですが、そうならない真空チャックを探しても見つかりませんでした。
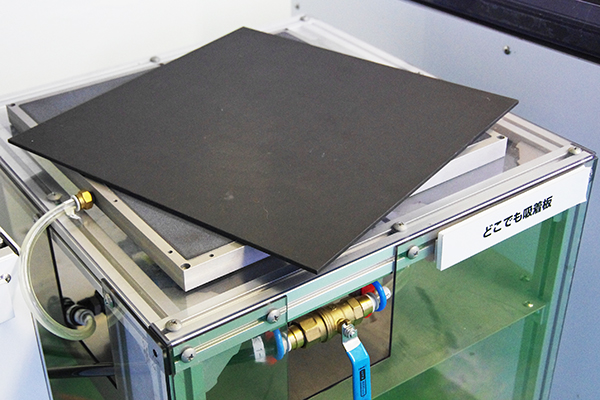
独自のセラミックス焼結技術により、内部発塵が皆無、気孔径・気孔率の自在制御が可能となることで、従来品における課題を解決する革新的な多孔質真空チャックを開発し、特許を取得している。写真は既存の真空チャックに置くだけで性能・機能を発揮するタイプの商品。
そこで、私はダイヤモンドの工具づくりが専門ですが、もともとの専門がセラミックスなので、眼に見えないくらい小さな穴が空いたセラミックスで真空チャックをつくることを、起業して2年目以降に始めました。というよりも、自分たちが工具を削るために、簡単に固定でき簡単に外せるテーブルがあればよいですよね。そこでセラミックスで真空チャックをつくり、工具を売るためにお客さんを呼んでテストすると、お客さんが「これは何?」「真空チャックです」「うちにもつくってくれないか」から始まり、「わかりました。どんなサイズですか?」と要望に応えるうちに、少しずつ、大きなサイズのテーブルを真空チャックとして出すようになりました。お客さんから頼まれて、すべてオーダーメイドで開発しました。そこに転機があって、よい方向に動いたのです。
― 「よい方向に動いた」とは?
真空チャックは、砥石業界とは真逆でした。つくるのに1ヶ月かかる点は同じとしても、売るのは数分で、結果も「固定できました」とすぐ評価できます。逆にそのような手離れのよいものをつくらないと、お金が回収できなかったのです。一方、真空チャックは1回購入するとずっと使えるので、砥石とは違ってリピート性がないというデメリットもあります。これも砥石と相反するところで、リピード性がないと、会社の将来が見えづらくなりますね。けれども、うちは小さな会社でしたし、小さなサイズから真空チャックを大きくしたことは、世の中であまりやっているところがなかったので、国内外の大手企業から使ってもらえるようになりました。
ただ、真空チャックを探しているお客さんが、真っ先にうちに来るかと言えば、ほぼ100%来ません。どんな経路でうちに来るかと言えば、普通はインターネットで探しても見つからない場合、最初は大手商社を介して業界大手に行くわけです。けれども皆さんが「できない」と言うから、その「できない」時、うちに来られる。そして「どんなことをしたいですか?何に困っているのですか?」と聞くと、やっぱり要望を言ってくれるわけです。
例えば、そもそも真空チャックは、穴が塞がれば(真空状態になって)吸着しますが、穴が塞がっていなければ(空気漏れを起こして)吸着しません。ですから、ワークのサイズは吸着盤と同じでないと吸着しないのは当たり前の話ですよね。ですから「テーブルが大きくて、どこにワークを置いても吸着できる真空チャックがほしい」というお客さんの要望は、「ワークを置いていないところから空気が漏れているのに、吸着できるわけがない。物理的に無理」というのが当たり前の話なのです。それで一旦は終わるのですが、「でも、そんなのがあったらいいですね」というお客さんの話を聞いて、逆に私は「なぜ空気が漏れたら、吸着しないのだろう?」と考えちゃうんです。「当たり前なのは理解しているけど、空気が漏れなかったらどうなるっけ?」とね。そうやって、ずっと想像を膨らませていくと、おもしろいアイディアが出てくるんです。「空気が漏れないことを"擬似的に"やればいいんだ!やってみよう」とね。私の合言葉は、「やってみよう」なんです。
◆ 失敗から新たなアイディアが生まれる
もうひとつ、おもしろい話があります。小さなサイズのセラミックスは、研究室でも簡単につくれます。けれども、テーブルサイズのセラミックスは、さぁ、どうやってつくろう? ここにも、たくさんの試練がありました。焼き物をする時はすべて、お茶碗でも何でも、台の上にものを乗せてつくります。大きなセラミックスをつくるためには、大きな台がなければできません。けれども世の中には1mの台しかないのに、2mの台がほしい時、1mの台を4つ並べて2mの台をつくろうとすると、割れてしまうのですよ。何回やっても、どんなやり方をしたって、割れるのです。その時が一番苦しい時期でした。
「テーブルサイズのセラミックスをつくってほしい」とある大手企業から頼まれて、一千万円以上もする大きな窯を購入しました。うちにとっては大投資ですよ。そして1週間に1回、窯開けをするのですが、「ああ、今回もひびが入っているなぁ...」と窯の蓋を閉める日々が続くのです。けれどもおもしろいのが、毎回毎回アイディアが出るんですよ。「なぜ割れたのだろう?」「そうか、ここが足りていなかったからか!」と、次の対策を打つ。次、釜に入れる時には皆で「よし、これ以上もうアイディアはない。全部入れ尽くした」と入れ、一週間後に焼き上がって窯開けをすると「わ!また割れてるし!!」。これを何回も続けるわけです。でも、アイディアは毎回出るんです。「失敗した!」「なぜ失敗したのだろう?」というところに、前回考えていなかったアイディアが出てきて、「アイディアは無限だなぁ」と思いました。
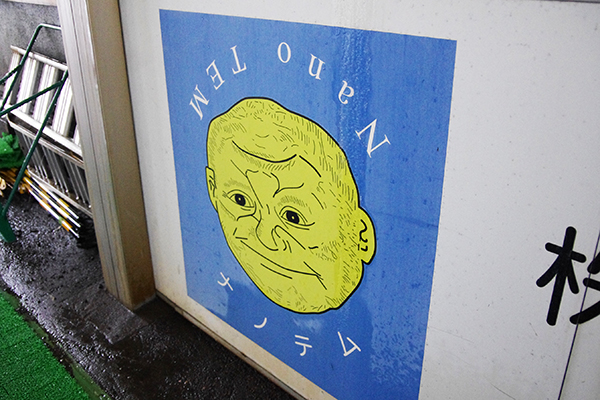
ナノテムのロゴマーク
もちろん、何でもできるわけじゃないですよ。できないことも当然あります。けれども、できるものの方が多いのではないかと私は思うのです。今まで当たり前だと思っていたことが、実は当たり前じゃないかもしれないぞ。既存の概念にとらわれず、別の方向から見れば、ものの見方は変わるはずだ。その想いを、当社のロゴマークで表現しています。180度回転すると怒った顔が笑った顔に変わって見えるでしょう? これがうちのポリシーです。
― どのようにしてテーブルサイズのセラミックスをつくれたのですか?
はじめは「4枚の台で焼き物をするしか無い」発想から始めていました。けれども「そもそもなぜ割れるのか?」を考えた時、ものは温度が上がると、ほとんどのものが膨張しますよね。台を並べると、温度が上がって膨張した時、台同士が接している点が競り合うため、向こう側に広がります。それが今度は冷える時、その部分に隙間が空くためにひびが入って割れてしまうのではないか。そのように理由を考えました。
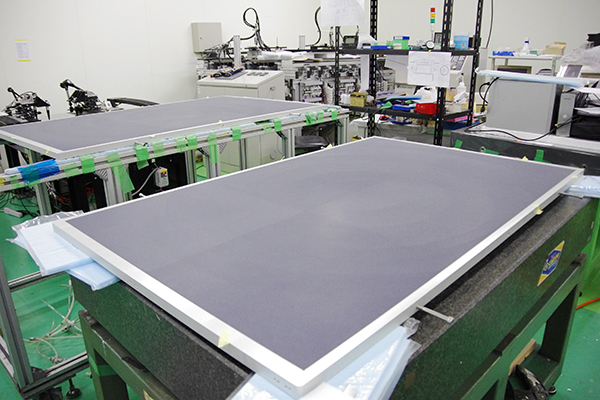
ナノテムの真空チャックは顧客の要望に合わせた仕様で最大2.5m角まで対応できる。
そこで私が打った手が、「じゃあ1mの台を使う発想をやめよう。これが50mm角のブロックならどうなるだろう?」でした。50mm角のブロックを並べた場合、これも全部膨張しますが、例えば、1m(1,000mm)のものが1mm伸びると膨張率は1/1000ですが、それが1cm(10mm)のものなら、同じ膨張率の場合、10μmですね。つまり、材料の立場から見れば、1mm伸びるのは痛いけれど、10μm程度だったら、痛くも痒くもないはずだ。それで実際に試してみたら、一発でうまくいきました。やっぱり、理屈は合っているな。誰も教えてくれない"屁理屈"ですからね。けれどもそこに解がありました。そのやり方で大きなサイズに変えてつくってみても、全部割れずにつくれました。以来、大きなサイズの真空チャックの依頼が来ても、「やれるぞ!」となりました。
― 真空チャックはどのような用途に使われているのですか?
用途としては、主に液晶・有機ELパネル製造装置用のテーブルに使われています。韓国の大手エレクトロニクスメーカーが大口顧客です。一方、日本のメーカーは冒険をしないという印象です。展示会で、「見積りが欲しい」と言われる時も、日本と韓国のメーカーでは全く反応が違います。「個数によって見積り金額は違いますよ」と話した時、日本のメーカーが求めるのは1個、さらに社内の了承を取るまでに半年から1年もかかります。一方で、韓国メーカーの場合、若い社員が自分で判断して、100個単位で見積もりし、2週間後には発注します。やはり冒険をしなければ、負けるのは当たり前ではないかと感じます。
◆ 課題をクリアすると、また新たな命題が生まれる
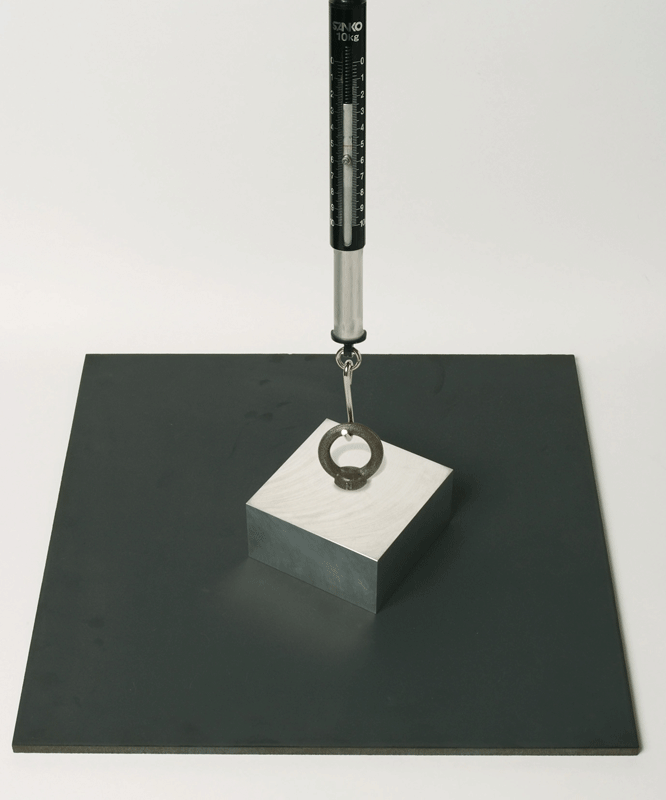
部分吸着が可能な真空チャック
ひとつのテーマをクリアすると、以前お客さんが言っていた「どこに置いてもくっつく吸着盤があったらいいな」という、次のテーマが出て来ます。部分吸着についても実現できる方法に気付きました。「空気が流れなければ駄目だけど、流れ過ぎても駄目なんだ。じゃあ機構の穴の経を小さくしたセラミックスをつくれば実現できるはずだ」と。すると、できちゃった、ということで特許を出しました。
スカスカ空気が漏れないようにする技術が、うちの特許技術です。空気が流れ過ぎても、流れ過ぎなくても駄目ですから、セラミックスの穴の経と距離で、空気の流れる抵抗を制御しよう、という発想です。すると、ワークが載っている下は真空になり、その周りから空気は漏れてはいますが、じわじわ流れると、一瞬一瞬を見れば、あたかもラップが載っているようになります。それが後付ですが、理屈です。「こういうことかな」と理由がわかると、次の攻め方がたくさんできるのです。
どこでも吸着版をつくると、今度は「どこでも吸着盤は欲しいけど、レーザーを当てたい」というお客さんがいました。レーザーを当てると、うちのセラミックスといえども傷がつくのです。私は「じゃあ交換してくださいよ」と思うけど(笑)、お客さんは「交換するのは嫌だ」と言うし、「レーザーの焦点深度を変えてください」と言っても、「変えられない」と言います。「じゃあ、レーザーでテーブル上のワークだけが切れて、テーブルには傷がつかなければいいわけですね」と、また新たな命題が生まれます。
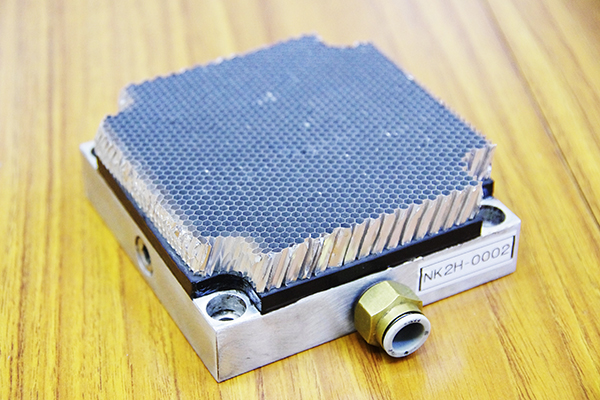
金属の穴を斜めにするアイディアで、CO2レーザーを当てても、下のセラミックス真空チャックは傷つかない。
世の中でよく使われているCo2レーザーは、金属が切れないという性質があります。そこで、レーザーが当たっても切れないで欲しい部分を金属にすればよいと考えました。ただし、吸着のために穴を開けると、穴からレーザーが下に届き、セラミックスは傷ついてしまいます。そこでどうしたかと言うと、じゃあ、穴を斜めにすれば、レーザーは下に当たらないぞ、と気付きました。これをうちのセラミックスの上に載せれば、成立です。これも今から売り出します。
◆ 夢の完全非接触浮上搬送や、絶対に動かない真空チャックも可能に
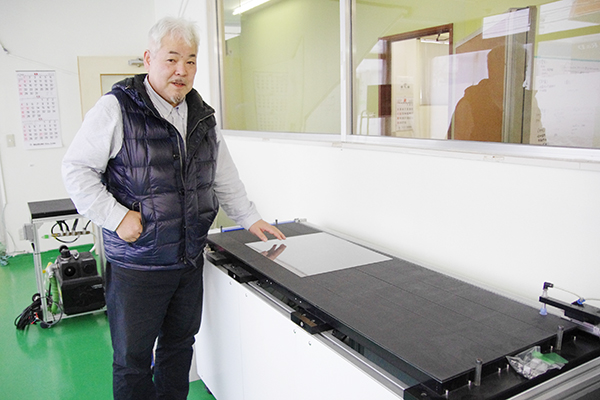
触っていなくても運べる、完全非接触浮上搬送装置
真空チャックについては、「くっつく」話の他に、「浮かせる」話もあるんですよ。真空を引いていたのとは逆で、今度はエアーを出し、吸着盤にワークを浮かせ、吸着盤上で次の工程に運ぶシステムです。ただ、ものは浮かぶけれど、くるくる回り、どこにでも行ってしまうのが欠点でした。やりたいことは、「浮かばせて、止めたい。ただし、触っちゃ駄目」です。さあ、どうやって固定しますか? と考えていきます。もはや禅問答の世界ですよ。「触らないで何とか固定したい」「できるはずがないだろう」から始まるのですが、これができるようになるのです。
― どのようにして可能にしたのですか?
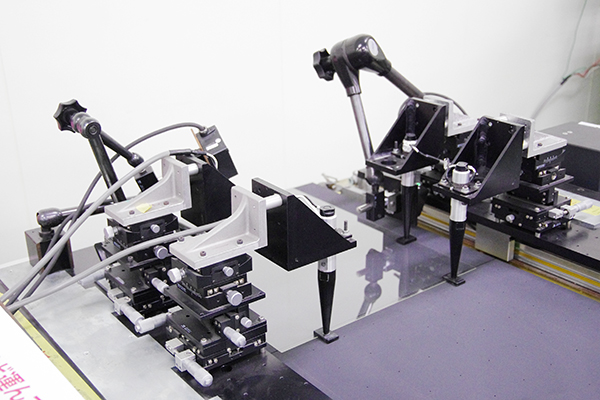
正圧と負圧それぞれのエアーをコントロールすることで、真空チャックからワークを浮かせる完全非接触浮上搬送を実現。
やれる方法がありましてね、ワークを非接触で支える4本の板に、蝶々の羽のような構造をつけて、超音波振動をかけると、目には見えないですが、蝶々の羽のように高速に羽ばたくのです。蝶々の羽はよくできていて、羽が下がった時に負圧となり、上がった時に正圧に変わるので、ワークをこの下に持ってくると、一番安定なところで止まります。すると、ワークを浮かしながら、手を離しても、引っ張っても、常に同じ場所に来ることを見つけたのです。このような仕組みで、正圧と負圧それぞれのエアーの供給と真空吸引をコントロールすることにより、空気で浮かせながらワーク姿勢を安定させることができました。言われてみれば、「なんだ、それだけか」と簡単に思えますが、つくってみればと言うと、皆つくれないのです。ガラスのような薄い材料でも浮かせられて、触らないのに、ヒューンと早く戻って位置も決まるし、便利そうでしょう? これまでやりたくてもできなかった夢の機能です。これから、この完全非接触浮上搬送装置が売れると見込んでいます。
もうひとつ、今最も新しい商品が「絶対に動かない真空チャック」です。先程の「どこでも吸着盤」も、真空を引いて、それなりに動かないのですが、無理矢理やれば動くのですよ。それでも絶対に動かないようにしようと今、新たに開発しています。これも単純な仕組みで、普通は摩擦係数が0.2や0.3程度で、摩擦係数1を超えるものはあまりないのですが、摩擦係数が1を超える材料があったらいいなという発想で開発して、もうすぐ売り出します。これは、本当の意味でのオンリーワンになれるかもしれません。私が欲しかった吸着盤は、まさにこの絶対に動かない吸着盤ですし、近所の加工屋さんだって皆、欲しがると思います。
ですから、はじめからテーマがあって真空チャックをやっているわけではないのですよ。砥石の方は、やりたいことがずっとありましたが、ずっと手を出せないのです。だって、真空チャックの方が忙しいのだもの。真空チャックの方は、性能も値段も、ほぼ他所に勝てるだろうというところまで来ました。年間売上高も今年6億円を超え、食える目処が付いてきました。
◆ 従来の欠点を全て解決する、理に適った工具づくり
冒頭にお話した通り、もともと私は工具をやりたくて起業しました。工具の欠点については、20年前からずっと私は不満に思っていました。先程も、「工具業界はベンチャー企業が参入できない欠点がある」と言ったでしょう? てっきり20年の間に進歩しているだろうと思ったら、まだ20年前の課題が課題のままでした。「なんだ、まだ参入できるじゃないか」と、今一生懸命、工具をやり始めたところです。従来の工具の欠点をすべてなくした、理に適った工具です。
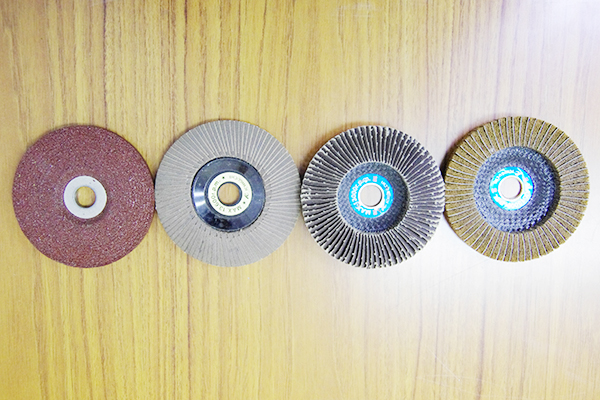
従来型の砥石
本当は大きな工具をつくるのですが、従来品の特徴を説明しやすいよう、一般のホームセンターで売られている普通の工具を今回準備しました。昔の工具は、砂がプレスで詰められていました(写真左)。けれども削るうちに、切り屑で目詰まりして切れなくなるという問題がありました。ですから、工具も少しずつ変わっていきました。左から2番目が、約25年前、私が工具メーカーに就職して2,3年後にできた工具で、サンドペーパーを重ねたタイプです。結構売れましたが、これも目詰まりの問題がありました。目詰まりしないようにするため、今度はサンドペーパーを砥石の面に対して垂直に並べた工具が登場しました(写真左から3番目)。けれども、これは使っていくうちに倒れるという問題がありました。そこで倒れにくくするために、今度はサンドペーパーの間を埋める工夫がされ(写真右)、今、売れていますが、これでもやっぱり倒れるという問題があります。
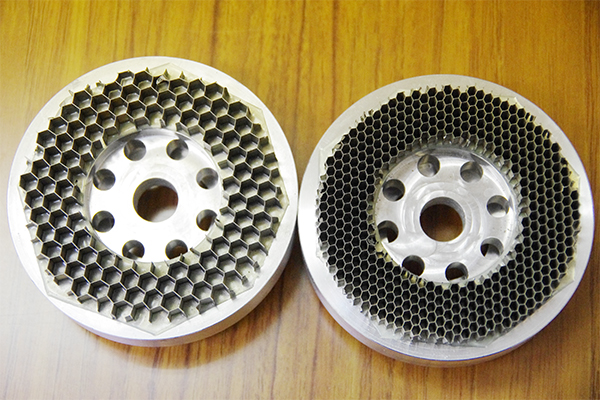
砥石のパターンニングによって分担荷重を制御可能に。
そこで、倒れずに、目詰まりもせずに、ずっと切れる工具にするにはどうすればいいか? を考えました。そこで私が考案するのがハニカム構造の砥石です。ハニカム構造にすることで、倒れないですし、切り屑がこの間に入るので、目も詰まらないです。従来品の何倍も切れます。私はいつも喩え話で説明するのですが、テーブルいっぱいに針を密集させると、その上を人が歩けますよね。では、その針の間隔が1cmに広がると、どうなりますか? 針が刺さって、足が血だらけになりますよね。従来品の砂でできている工具は、砥石の全面が切れるものでできていました。一方、私が考案した工具は、このハニカム構造の柱部分にしか、ダイヤなり切れるものがない構造です。先程の剣山の間隔を広げた喩え話と同じでしょう? 「砥石にパターンニング性を持たせよう」というのが、私がずっと考えてきたことです。
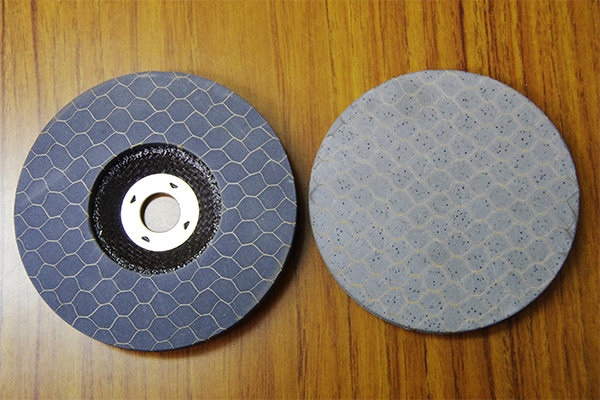
コア部分とダイヤ部分の構成を自在に設計でき、砥石の能力を最大限に引き出すことができる。
「けれども、ハニカム構造の中にゴミが詰まるのでは?」って、言われると思いましたよ。そこで、ハニカムの中を埋めました。ダイヤの柱の部分よりも、この灰色のコア部分が弱ければ、常に柱の方が飛び出るので、柱で切れます。セラミックスでも何でも、バリバリ削れます。これで、世の中の工具がガラッと変わるでしょう。いよいよ今年3月、ドイツで砥石デビューを果たします(注:取材は同年1月に実施)。
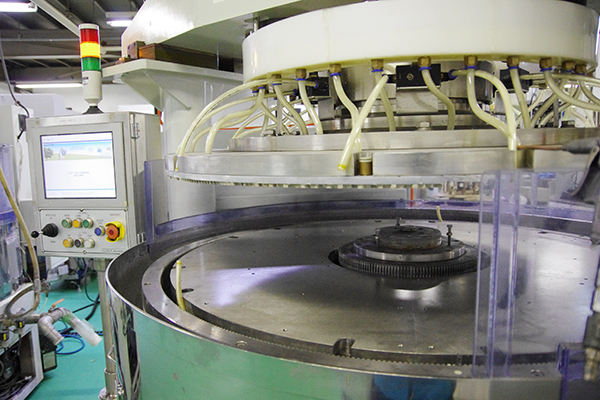
砥石内部からの水・エアー供給により高精度を実現
もうひとつ、秘密兵器があるのです。この灰色のコア部分には、実は、「多孔体」という、目には見えない小さな穴が空いています。普通は加工する時、熱くなるので、加工屋さんは水をかけながら削ります。けれども、ある速さ以上で回転しているところに水をかけると、水は跳ね返りますよね? じゃあ、絶対に水がかかる方法を考えましょう。そこで考えたのが、工具内部から水が出れば、削っているところに絶対に水がかかるという方法です。実際に見てもらうと、工具全面から水が出ているのがわかるでしょう? 水だけでなくエアーも出せます。
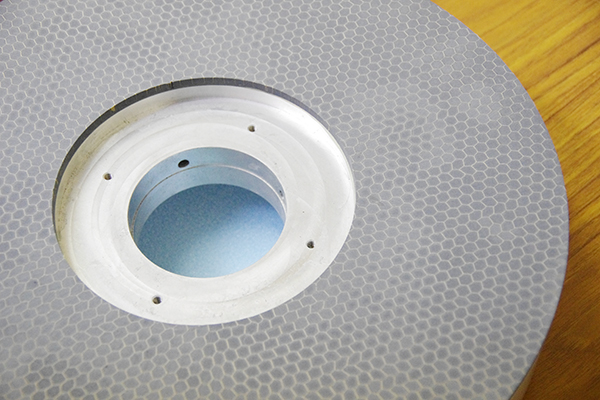
コア部を水により膨張させることで、荒砥から仕上げまで同じ砥石で対応することも可能。
さらに、この工具は、水を含むと、灰色のコア部分が膨らみます。ですから真空を引きながら、まずハニカム構造のダイヤ部で加工して荒加工し、水を出すと、灰色のコア部分が膨らんでピカピカに磨けてしまう。そんな一挙両得を狙った工具です。
要は、先程も少しお話しましたたけど、「ワークの気持ちになれ」ということなのです。削られている材料の方からすると、「水、かかってねぇから!」って、思っていたんですよ(笑)。けれども、多くの人はそこまで考えていなくて、「そういうものだろう」と思い過ぎているのです。先程のロゴマークと同じで、「いやいや、当たり前じゃないぞ。ものの考え方を変えよう」というのが、私の工具づくりのモットーです。理に適った工具づくりを20年間、ずっと私は我慢して温めてきました。これがやっと今年からデビューし、どんと見事に売れ始めたら、「オンリーワンです」と強気に言えるかもしれないです。
◆ 「なぜ、そんなことで悩んでいるの?」と、口で言うだけなのは嫌い
ですから、オンリーワン企業になった軌跡がどうこうというよりも、起業した、イコール、辞めたくても辞められないから、もう、ひたすら食っていくためにはどうするか?をずっと考えるほかありませんでした。人のやらないことを狙ってやったわけではなく、人がやらないことをたまたまやってきただけです。
人ができないことを「なぜ、そんなことで悩んでいるの?」と口で言うだけなのは、私は嫌いなんです。それを具現化するには、自分でやるしかないぞ、ということです。手を動かしてやってみて、失敗して、でも失敗してもアイディアは出るから、諦められない、だから考える、その繰り返しです。最後にすべては解決できないですが、それでも結構多くのことは解決できますよね。追い求めれば、実は解が見えてくるのです。
うちの社員にも、「はじめは屁理屈でもいいから、常にその行動を選んだ根拠を持て」とよく言います。例えば、「右と左、どちらに雨が降るか?」という時、できない方向に進む人に共通する思考パターンは、「どちらにしようかな?」と「天の神様が言う通り」に進み、雨が降っても、「まぁいいか」と諦めることを繰り返すパターンです。「よくわからないけど、とりあえず、まぁいいか」で動くと、自分の行動に根拠がないので、同じシチュエーションでまた延々と同じことの繰り返しです。ですから「まぁいいか」の人は、延々とステップを登れず、同じ場所に居続けるのです。
私は違います。「右が明るいから、晴れている可能性がある。だから私は右を選んだ」と根拠を持って行動します。それで雨が降ったとしても、「前回、私は明るいから選んだが、あれは間違いだった。だから今度は暗い方を選ぶ」と選びます。それでまた失敗するかもしれませんが、でも明るい方がよいのか、それとも暗い方がよいのか、それが探し求める行き先へと徐々につながります。ステップを一段登るためには、理屈をつけることです。それが間違っていてもいいんですよ。ステップアップができれば。
私が追い求めるのは、「なるほどね」という根拠です。「なるほどね」の次には「じゃあ、次こうしよう」という次の展開が見えます。それを追い求めていくと、人は成長すると思います。すみません、変なことを言いましたけど、でも私は重要だと思うのです。そういうことを考える人が、どこへ行っても一人でも生きていける、人間力のある人になれると、私は信じています。
社長が二十歳だった頃
― 次に、髙田さんが二十歳だった頃について、教えてください。
◆ 国立大学発ベンチャー第1号として起業するまで
二十歳だった頃は馬鹿ですよ(笑)。うちの兄弟が大学に進学したので、自分も何となく進学しただけで、何の目的も目標もなかったです。私は熊本県八代市生まれで、地元の八代工業高等専門学校を卒業後、兄と同じ長岡技術科学大学に編入学しました。私には、長岡に来る理由がありました。兄と一緒にお金を出して買った車に乗る、という変な理由が(笑)。
当時、何を考えていたか? 勉強をして、お金を貯めて、遊ぶことしか考えていなかったです。ただ、メリハリははっきりしていました。徹底して遊ぶし、勉強すると決めたら他のことはシャットアウトして徹底的に勉強しました。スキーも長岡に来てから覚えましたし、アルバイトも色々なことを経験しました。将来何をやりたいかは全く考えておらず、漠然と「きっとサラリーマンになるのだろう」くらいしか思っていませんでした。
その後が波乱万丈で色々あったのですが(笑)、大学卒業後は研究生として1年間研究室に残りました。長岡技術科学大学では「実務訓練」という、今で言う、インターンシップの制度がありました。その制度を利用して半年以上、四国の砥石メーカーである株式会社日本グレーン研究所で砥石について学んだ後、同学大学院に進学し、多孔体をテーマに修士論文を書きました。
― 学部生の頃は、多孔体についての研究はしていなかったのですか?
学部時代は、多孔体とは逆の「緻密体」という、世界一強いセラミックスをつくる研究をしていました。世界一強いセラミックスをつくると、加工できる工具がないのです。そこで、実務訓練では四国の工具メーカーを選び、大学院修士課程修了後に、同社に就職したのです。ところが、工具は工具で、経験と勘しかない世界で、理に適っていないことに、私は不満を抱きました。堅い素材を削るにはダイヤモンドなどを使う必要がありますが、ダイヤモンドが潜在的に持つ加工能力を100%使い切っていなかったのです。
そこで、その工具メーカーに5年間勤めた後、長岡技術科学大学に助手として戻り、研究を進める中で実現したのが、独自のセラミックス焼結技術でした。この技術を活用すれば、工具の加工能力は従来の2~3倍に高まります。その"屁理屈"を自分自身で実証したいと思い、大学に戻ってから3年後に起業しました。そしてこれまで20年間ずっと走り続けてきました。その割には、ちっとも痩せないですが(笑)。けれども、もう少しうまく行けば、本当の意味でのオンリーワン企業になれるのではないかと手応えを感じています。
成功してあぶく銭ができたら、次にやりたい夢はベランダ菜園ですね(笑)。多孔体を使って菌を上手く飼い、ベランダサイズで自給自足できることが理想です。最後はやっぱり、衣食住ですからね。そういう"遊び"をぜひやりたいものです。
我が社の環境自慢
― 続けて、貴社の環境自慢を教えてください。
◆ 早寝早起き推奨、飲める人は大歓迎
飲める人は大歓迎です(笑)。それと、早寝早起きを推奨しています。朝一番から仕事を始めて、午前中には仕事を終え、午後は翌日の準備をしてから、まだ明るいうちに家に帰り、ビールを飲むくらいが、私は効率がいいと思うのです。なかなかその想いがまだ社員全員には浸透していないのですが...。
若者へのメッセージ
― 最後に、今までのお話を踏まえて、若い世代へメッセージをお願いします。
◆ 自分に限界をつくるな
自分で「これが限界だ」と線を引いた瞬間に、自分で自分自身の成長を止めてしまいます。「死ぬ気で」と言っても絶対に死なないですから、死ぬくらい、やってみればいいんですよ。「できない」と否定しても、何も始まりません。「できない」から始まり、失敗して、そこに活路が見えて、「できた」喜びをぜひ知ってほしいです。その喜びを一度味わえば、次も絶対にやってみれますから。だから、まずは「やってみよう」が大切ですよ。
― 髙田さん、本日はありがとうございました。
社員に聞く、我が社の環境自慢
◆ 世の中にないものを売る魅力
/五十嵐 陽香さん(23歳、入社5年目、新潟県長岡市出身)
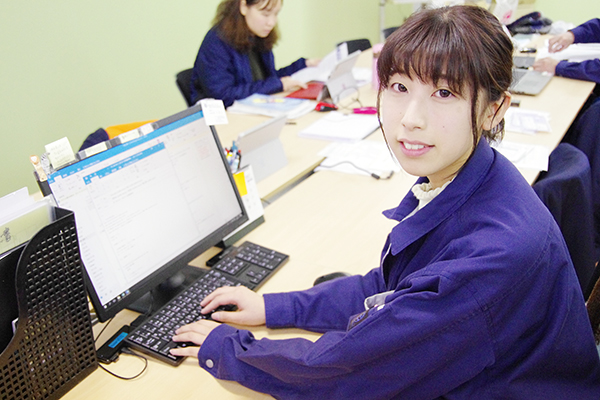
高校卒業後に当社に入社し、今年で5年目です。主に事務関係を中心に、輸出や発注業務、お客様とのメール対応のほか、2年前からは営業もやらせてもらっています。入社する時も、当社の「世の中にない商品を独自に開発している」点に惹かれましたが、今でも展示会などでお客様から「これはすごいね」「初めて見た」と驚かれるたびに私も嬉しさを感じています。世の中にないものを売っている環境が刺激的で楽しいので、それが我が社の自慢です。今年3月には、ハニカム砥石の第一号がドイツの展示会でデビューします。まだまだ私は勉強中の身ですが、難しい知識も自分なりにわかりやすく読み解きながら、これからも独創的な社長と一緒に頑張っていきたいです。
◆ 新しいことにチャレンジできる環境が魅力
/NGUYEN HA(グエン ハー)さん(28歳、入社1年目、ベトナム出身)
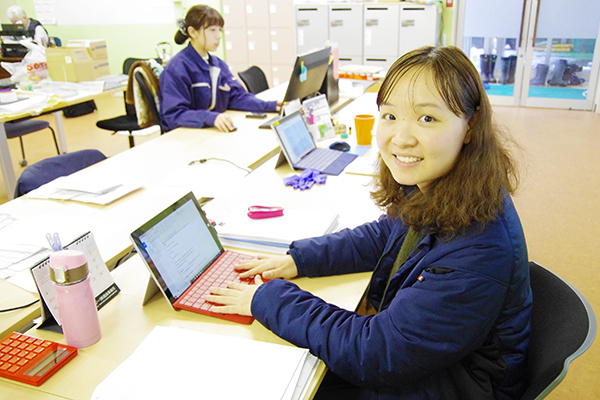
私はまだ入社して3ヶ月目ですので、今は色々な仕事に参加しています。例えば展示会の仕事、開発の作業、営業関係の仕事も少し入っています。私は技術に興味があります。砥石やセラミクスのことはこれまでよく知りませんでしたが、ナノテムの商品を実際に触って、これはすごいと思いました。今の仕事内容は前職とは全く異なりますが、私はチャレンジしたいタイプですので、ナノテムで働くことを決めました。ナノテムの皆さんはいつも優しく仕事を教えてくれるので、とてもありがたいです。これから日本語も勉強しながら、得意な英語(TOEIC 980点/990点満点)とベトナム語を活かし、海外のお客さんに営業をたくさんしたいです。
◆ 一言で言えば、成長できておもしろい環境
/髙田 愛梨さん(23歳、入社1年目、新潟県長岡市出身)
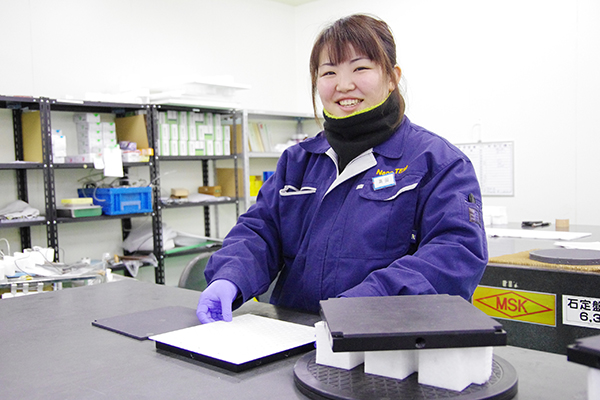
名前を見ておわかりのように、社長の娘です。2017年度に大学を卒業後、当社に入社しました。現在は現場での開発業務や、社長から指示されたことの実践をメインに、入社1年目ですので現場の作業を一通り覚えている段階です。少し前までは父の会社に入社すると思っていませんでしたが、海外にも輸出し、世界の名だたるメーカーに製品を納めていることを知って、当社のすごさを少しずつ理解しているところです。実際に開発に携わってみると、まだまだわからないことの方が多いですが、私は新しいことにチャレンジしたい性格なので、色々な勉強をしながら仕事ができる環境が、当社のよいところだと思います。また、出社時間や退社時間も一般的な企業では9時から18時が多いと思いますが、当社は朝7時半には来て16時半には帰宅することを推奨しています。夜の時間を有意義に使おうという考え方も、すごくおもしろいと思います。常日頃おもしろさを感じていますが、我が社の環境自慢を一言で言うとすれば、「成長できて、おもしろい環境だよ」というのが一番強いですね。今は技術開発を担当していますが、うちの会社はこれから営業がメインになると思いますので、私も技術を勉強した上で、「どこでも吸着盤」や「ハニカム砥石」を、さらに多くの人に知ってもらえる働きをしていきたいです。
コラボレーション
おすすめ記事
![]() |
【特集】宮城の研究施設 一般公開特集 |
![]() |
【特集】仙台市総合計画審議会 仙台の10年をつくる |
【社会】社会って、そもそもなんだろう?

青井真さん(防災科学技術研究所)に聞く:<東日本大震災から10年>東北地方太平洋沖地震が起きて、地震研究はどう変わった? 2021.11.11 【大草 芳江|社会って、そもそもなんだろう?|科学って、そもそもなんだろう?|防災科学技術研究所】

前田拓人さん(弘前大学)に聞く:<東日本大震災から10年>もし東北地方太平洋沖地震が起きていなければ、地震研究はどうなっていた? 2021.10.08 【大草 芳江|弘前大学|社会って、そもそもなんだろう?|科学って、そもそもなんだろう?】

日野亮太さん(東北大学)に聞く:<東日本大震災から10年>もし東北地方太平洋沖地震が起きていなければ、地震研究はどうなっていた? 2021.10.02 【大草 芳江|東北大学|社会って、そもそもなんだろう?|科学って、そもそもなんだろう?】
同じ取材先の記事
◆ ナノテム

【オンリーワン企業がオンリーワンたる所以を探る Vol.20】独自のセラミックス焼結技術で、生産現場の生産性を向上/ナノテム(新潟県長岡市)社長の髙田篤さんに聞く 2018.05.01 【大草 芳江|ナノテム|公益財団法人東北活性化研究センター『”キラリ”東北・新潟のオンリーワン企業』Collaboration連載企画|社会って、そもそもなんだろう?】
社会って、そもそもなんだろう?
最新5件
カテゴリ
取材先一覧
■ 幼・小・中学校
■ 高校
- ・仙台一高 (15)
- ・仙台二華 (14)
- ・仙台二高 (12)
- ・仙台城南高校 (5)
- ・仙台城南高等学校 (0)
- ・仙台高専 (4)
- ・宮城一高 (4)
- ・宮城県高等学校理科研究会 (2)
- ・岩ケ崎高 (1)
- ・東北工業大学高校 (0)
■ 大学
■ 国・独立行政法人
- ・内閣府 (1)
- ・宇宙航空研究開発機構 (5)
- ・文部科学省 (0)
- ・東北経済産業局 (17)
- ・水産総合研究センター東北区水産研究所 (1)
- ・理化学研究所 (3)
- ・産業技術総合研究所東北センター (36)
- ・科学技術振興機構 (1)
- ・防災科学技術研究所 (1)
- ・高エネルギー加速器研究機構 (1)
■ 自治体
- ・仙台市 (8)
- ・仙台市博物館 (4)
- ・仙台市天文台 (12)
- ・仙台市教育委員会 (13)
- ・仙台市産業振興事業団 (1)
- ・仙台市科学館 (8)
- ・仙台文学館 (2)
- ・仙台管区気象台 (2)
- ・塩釜市 (3)
- ・宮城県 (8)
- ・宮城県古川農業試験場 (2)
- ・宮城県教育委員会 (1)
- ・宮城県農業・園芸総合研究所 (1)
- ・気仙沼市 (1)
- ・登米市 (1)
■ 一般企業・団体
- ・DIC株式会社 (2)
- ・K sound design (1)
- ・KDDI (2)
- ・natural science (1)
- ・せんだい・みやぎNPOセンター (2)
- ・てとてと (1)
- ・ひのき進学教室 (11)
- ・みやぎ工業会 (8)
- ・みやぎ工業会会長 (0)
- ・みやぎ産業振興機構 (3)
- ・アスター (1)
- ・インスペック (1)
- ・エツキ (1)
- ・ソニー (3)
- ・ソニー教育財団 (1)
- ・ソフトバンク (1)
- ・ティ・ディ・シー (1)
- ・デュナミス (1)
- ・ドットジェイピー (1)
- ・ナノテム (1)
- ・ハリウコミュニケーションズ (3)
- ・ハード工業有限会社 (1)
- ・フジイコーポレーション (1)
- ・プレファクト株式会社 (1)
- ・ヤマダフーズ (1)
- ・全国学習塾協会 (3)
- ・公益社団法人セーブ・ザ・チルドレン・ジャパン (1)
- ・勝山酒造部 (1)
- ・及源鋳造株式会社 (1)
- ・大武・ルート工業 (1)
- ・太白少年少女発明クラブ (1)
- ・宮城の新聞 (0)
- ・宮城県中小企業家同友会 (1)
- ・宮城県産業人クラブ (0)
- ・宮城県職業能力開発協会 (1)
- ・宮城県酒造組合 (2)
- ・工藤電機 (2)
- ・平孝酒造 (1)
- ・応用物理学会 (2)
- ・新東総業株式会社 (1)
- ・日刊工業新聞社 (7)
- ・日本アンドロイドの会 (1)
- ・日本技術士会 (2)
- ・日本私立大学団体連合会 (1)
- ・日本農芸化学会東北支部 (1)
- ・日本IBM (3)
- ・日東イシダ (1)
- ・有限会社 柏崎青果 (1)
- ・東京エレクトロン宮城 (1)
- ・東北ニュービジネス協議会 (1)
- ・東北活性化研究センター (3)
- ・東北経済連合会 (1)
- ・東北電力 (2)
- ・東北電子産業株式会社 (1)
- ・東栄科学産業 (1)
- ・林精器製造 (1)
- ・株式会社三栄機械 (1)
- ・株式会社悠心 (1)
- ・河北新報 (1)
- ・神田産業株式会社 (1)
- ・秋田化学工業 (1)
- ・笹氣出版印刷 (1)
- ・米鶴酒造 (1)
- ・萩野酒造 (1)
- ・農芸化学会 (1)
- ・遠藤工業 (1)
- ・鈴木製作所 (1)
- ・阿部蒲鉾 (1)
- ・阿部蒲鉾店 (1)
- ・鳴子の米プロジェクト (1)
- ・NECトーキン (1)
特別企画 「宮城の塾」
![]() |
学習塾から見る 宮城の教育の「今」 塾選びに一役 |

![]() |
【科学って、そもそもなんだろう?】 若手研究者座談会「地震学×情報科学の融合で得られたもの」 2024.09.16 |
![]() |
【科学って、そもそもなんだろう?】 地震の発生予測に挑む(京大防災研の西村卓也さん・京大名誉教授の平原和朗さんに聞く) 2023.01.26 |
![]() |
【社会って、そもそもなんだろう?】 【同窓生に聞く#01】中鉢良治さん(元ソニー社長、産総研最高顧問)がリアルに感じていることって、何ですか? 2022.10.27 |
![]() |
【科学って、そもそもなんだろう?】 地震学×情報科学の融合で、目指すは天気予報の地震版 2022.04.13 |
![]() |
【社会って、そもそもなんだろう?】 「仙台の地形と水との関わり」~地形から見る仙台の過去・現在・未来~ 2022.03.02 |
![]() |
【科学って、そもそもなんだろう?】 青井真さん(防災科学技術研究所)に聞く:<東日本大震災から10年>東北地方太平洋沖地震が起きて、地震研究はどう変わった? 2021.11.11 |
記者ブログ
![]() |
ひとり新聞社「宮城の新聞」の大草よしえが衆院選に立候補 2021.10.19 |
![]() |
最近の活動は「Twitter」に移行しました 2019.11.01 |
![]() |
【追記】テレビ朝日「モーニングバード」スタジオ生出演&iCAN'15世界大会(アラスカ)世界第1位! 2015.06.19 |
![]() |
2014年の振り返りと、2015年の抱負 2015.01.05 |
![]() |
平成25年度を振り返りました・・・。 2014.04.02 |
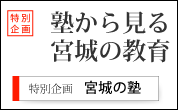
![]() |
中野塾(泉中央・北高森) |
![]() |
ひのき進学教室(泉中央・長命ヶ丘・八幡教室・上杉教室) |
![]() |
夢学館(東照宮・福室) |
![]() |
早稲田育英ゼミナール(泉中央) |
![]() |
ソーメック個別学習院(若林区、太白区、泉区に6教室) |
![]() |
明和塾(北山・八木山) |
![]() |
JUKU ペガサス仙台南光台教室(南光台南) |
アクセスランキング
- 【宮城の塾】 宮城の塾 仙台市を中心とした学習塾・幼児教室・進学塾の特集
- 世界中の研究者が憧れる研究拠点へ/東北大学WPI-AIMR本館竣工記念式典/科学って、そもそもなんだろう?
- [vol.1] 第1回宮城の日本酒を楽しむ会/社会って、そもそもなんだろう?
- 「仙台の地形と水との関わり」~地形から見る仙台の過去・現在・未来~/社会って、そもそもなんだろう?
- 宮城県仙台第一高等学校/教育って、そもそもなんだろう?
- 【宮城の塾】 ひのき進学教室(泉中央本部教室・八幡町教室・上杉教室・五橋教室・長町教室・愛子教室・吉成教室・大和町教室、他)
- 地震の発生予測に挑む(京大防災研の西村卓也さん・京大名誉教授の平原和朗さんに聞く)/科学って、そもそもなんだろう?
- 【宮城の塾】 JUKU ペガサス仙台南光台教室
- 【宮城の塾】 質問できます!/宮城の塾|宮城の新聞
- 【宮城の塾】 明和塾(北山教室・八木山教室)