取材・写真・文/大草芳江
2018年04月09日公開
「まずはやってみる」の開発力で
世界中が使いやすい製品を追求し、
トレッドミルと自動ネジ供給機でオンリーワン
株式会社大武・ルート工業(岩手県一関市)
代表取締役 太田 義武 Yoshitake Ohta
公益財団法人東北活性化研究センター『"キラリ"東北・新潟のオンリーワン企業』Collaboration連載企画 (Vol.17)
岩手県一関市に本社を構える株式会社大武・ルート工業(1968年設立、従業員48名、資本金4,000万円)は、高い開発力を武器に海外事業も展開する、オーダーメイドのトレッドミル(ランニングマシン)並びに自動ネジ供給機の国内トップメーカーである。オーダーメイドトレッドミルの設計から製造まで一貫生産が行える国内唯一の専門メーカーであり、また、世界で初めて「レール交換方式」を考案した同社の自動ネジ供給機は国内トップシェアを誇る。1999年「第11回中小企業優秀新技術・新製品賞」、2006年「文部科学大臣表彰 科学技術賞」、2008年 経済産業省「元気なモノ作り中小企業300社」等の賞や認定を受けている。そんなオンリーワン企業である大武・ルート工業がオンリーワンたる所以を探るべく、代表取締役の太田義武さんに話を聞いた。
オンリーワン企業になるまでの軌跡
― はじめに、貴社がオンリーワン企業と言われる所以を教えてください。
◆ 自動ネジ供給機とトレッドミルの国内トップメーカー
当社ではふたつの事業を営んでおり、どちらも参入企業の少ないニッチ市場で自社製品を開発・製造しています。
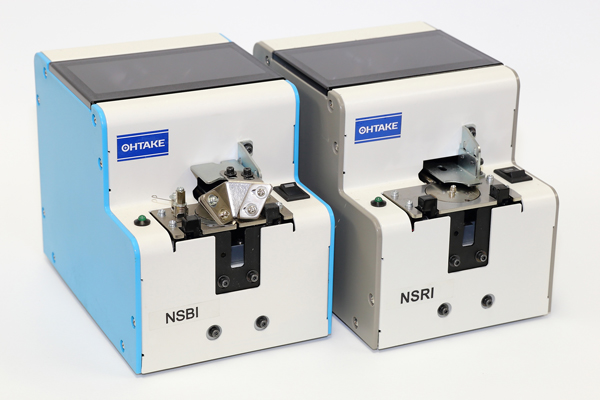
自動ネジ供給機
ひとつ目の事業は「自動ネジ供給機」の製造です。製品組立ラインにおけるネジ締め作業の効率を高める自動ネジ供給機に、世界で初めて「レール交換方式」を採用し、1台で複数径のネジへの対応を可能としました(ネジ自動供給機分野でトップシェア)。ユーザーは弱電(主として通信・家庭電気用品等を扱う部門の通称)から自動車、住宅建材まで、ネジを扱う工場すべてが対象となります。世界中で使いやすい製品を目指したことで、現在は30カ国以上で利用されています。近年ではロボット組立用としての需要も伸びています。
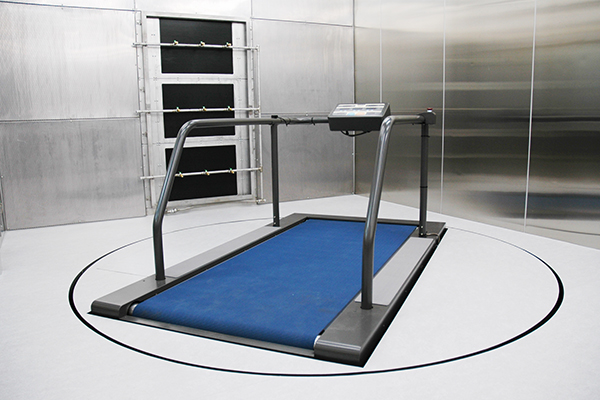
全天候型トレッドミル
もうひとつの事業は、トレッドミル(ランニングマシン)です。当社は日本国内で唯一、オーダーメイドのトレッドミルの設計から製造まで一貫生産が行える専門メーカーです。医療機器製造認定工場となっており、医療用や研究用等の特殊品を主に製造しています。これまで多くの大学や国の研究機関、医療機器メーカー、民間企業の研究チームやプロアスリートチーム等からご用命いただいています。
― そこに至るまでの過程を教えていただけますか?
◆ 下請けから脱して自社製品開発へ
弊社は1968年に設立し、大手電動工具メーカーのバンドソー(木材をカットして加工する小型の製材機)のOEM(相手先ブランドによる生産)からスタートしました。バンドソーはもともと製材業を営む父が開発したもので、私が会社を設立して製造・販売することになったのです。私が24歳の時でした。
当初はかなりの台数を売り上げ、順調に事業が進んでいましたが、そのうち原価低減を繰り返し要請されるようになりました。OEM発注元の大手企業が泊りがけで当社の製造現場に立ち入り、原価低減の方法や品質管理、品質保証等の指導を受けました。「部品をバラせば何千点あるのだから、そのネジひとつ1円ずつコストダウンすれば可能でしょう」と指導され、大幅な原価低減を受け入れましたが、最終的には「原価をさらに2割安くしなさい」と言われてしまいOEM継続を断念しました。
OEMを辞めた後は、自社製品ではなく付加価値の低い製品の下請けの仕事を2、3年、やってみたものの、もう懲りました。夜中でもお構いなく発注元企業から電話が鳴り続け、散々嫌味も言われ、嫌な思いを沢山しました。納期に間に合わせるために、社員も大変で、社員の親からは「うちの息子を家に返してくれ」と言われたこともありました。下請けの仕事の数自体はいくらでもありましたが、相手の都合でものをつくることに虚しさを感じました。「やはり自分たちでつくった製品でなければダメだ。何とか自分たちの製品をつくろう」と固く心に決めて以来、今でも基本的には下請けや部品製造の仕事はやらない方針です。
◆ 木材加工の技術を活かしてトレッドミルを開発
― 下請けから脱して、自分たちの製品として何から作り始めたのですか?
バンドソーで培った木材加工の技術で、最初は、警察犬用の犬小屋の製造を始めました。外壁を外せたり折り畳めたりする特殊用途の犬小屋をつくったところ、高額で売れました。ただ、量産化や錆の問題が解決できなかったので、別の製品をつくれないかと考えていた時、テレビでたまたまドックランを見て「うちで犬用のトレッドミルをつくれるな」と思い付きました。ところが犬用のトレッドミルをペット業界に売り込むと、「絶対にニーズはない。だって愛犬家は犬を連れて散歩したいのだから」と言われました。今では台湾等のメーカーがドックランナーを販売しています。時代の変化ですね(笑)。
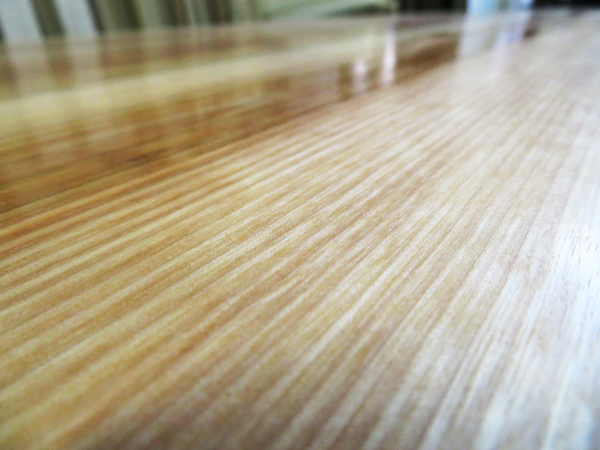
天然木材の走行板
そのうち、犬用から人間用のトレッドミルを製造するようになりました。今でこそトレッドミルはスポーツジム等にあって当たり前の存在ですが、当時の日本ではまだまだ真新しい存在で、そのほとんどが海外製でした。ある時、国内大手スポーツジムから「使用している米国製トレッドミルに問題が見つかったので、何とかしてもらえないか」と相談を受けました。他社の製品を直してあげることもできないので、本当に大変でした。試行錯誤する中、もともと製材業を営んでいた父からの木材加工技術に関する助言がブレイクスルーとなり、走行板に天然木を使う独自技術を生み出し、当時の既存品にあった様々な問題を解決することができました。他社の走行板には合板や金属、化学材料等が使われていますが、当社は、木材の持つ性質をうまく活かして磨き込むことで、安定して低動摩擦な走行板を実現することができたのです。使い込むことで滑らかになる木材はメンテナンスフリーで、潤滑剤の飛散もなく、耐久性が高いという特長があります。天然木を使用したオリジナルの低摩擦走行板は、今も当社製品の差別化要因となっており、それが医療現場や研究機関等から選ばれている理由になっています。
◆ 医療用や研究用のトレッドミル製造に特化
トレッドミル販売開始当初は、国内の需要があり販売は好調でした。ところが、しばらくすると、台湾や中国から安い製品が大量に輸入されるようになりました。そこで、スポーツ用のトレッドミルから、医療や研究開発用途の高付加価値商品に特化する戦略へ切り替え、難関と言われる医療用トレッドミルの許可を取得し、製造を開始しました。
けれども、その後も色々と大変でした。スポーツ器具メーカーが医療機器を製作したことで、それまで取引していた国内大手スポーツジムからの受注がゼロになってしまいました。競合しない業種だと思ったので、商売の難しさを感じましたね。実は一時期、トレッドミルをやめようと思ったこともありました。医療用の受注は月に数台はありましたが、特注品は時代の流れの影響を大きく受けるため、受注がない時期もあったからです。それでも結局、トレッドミルの事業を続けた理由は、思い入れがあり、何となくやめきれなかったのです。その間、トレッドミルの他にも事業の柱が欲しいと思い、自動ネジ供給機の開発に注力しました。そして気付けば、日本国内にトレッドミル専業メーカーは他にほとんどいなくなっていました。現在、特に医療用や研究用等の業務用の場合、目的や用途等に応じてきめ細やかな設計が必要なオーダーメイド製品のため、国内市場の業務用トレッドミルのほとんどを当社が開発から請け負っています。あの時、途中でトレッドミルをやめなくてよかったです。
◆ トレッドミルと無関係の自動ネジ供給機を開発
― もうひとつの事業の柱として、なぜ自動ネジ供給機にしようと思ったのですか?
トレッドミルを製造していた時、部品を安く仕入れるため、台湾に事務所を設けました。そこで働いていた台湾人社員の知り合いから、「自動ネジ供給機をつくってくれないか」という依頼があったのです。話を聞いてみると、台湾での電機・電子関連の工場で生産が急拡大する中、日本製で高性能のネジ供給機は既にあったそうですが、「日本のネジは精度が高過ぎて、公差が粗い台湾のネジでは途中で装置が止まってしまう。どんなネジでもスムーズに流れる自動ネジ供給機をつくってほしい」という話でした。
― トレッドミルとネジ供給機、全く違う機械に見えますが、技術面等で何か共通点はあるのですか?
全くありません(笑)。考え方も作り方も生産体制もお客様も管理方法も何もかもが全然違います。開発も本当に大変でした。そもそもネジって難しいんですよね。螺旋があるから、途中で引っかかってしまうんです。さらに大変だったのが、既成のネジ供給機が"特許の塊"だったことでした。特許を回避しながら、途中で詰まることなくネジを供給するにはどうすればよいか、非常に苦労に苦労を重ねながら開発を進めました。そして試作機が完成すると、件の台湾人の方が製造現場で実際に試し、問題の洗い出し等をあらゆる環境で一斉に行ってくれました。そのフィードバックを受けながら試行錯誤すること約2年。やっと製品化にこぎつけ、1996年にネジ供給機第一号の販売を開始することができました。機構設計は私一人で考えて、その後の量産設計は社員が考えてくれました。とはいえ、それまでトレッドミルという大型の機械しかつくっていなかったので、社員は皆、頑張ってくれましたね。
ところが、販売を始めた当初、国内では、名も知られていない我々の装置は、販売代理店から全く相手にしてもらえませんでした。そのため、海外での販売からスタートしました。テストを海外で行っていた関係で、海外の販売代理店が取扱説明書等の翻訳面でも協力してくれたこともあり、まず海外で売れ始めました。海外では「大手企業だから、ベンチャー企業だから」という理由で取引先や製品を選ぶという考え方がないようです。すると最初は販売を断ってきた国内の販売代理店から、「日本で知名度のない製品がなぜ海外で使われているのだ?自分たちも日本国内で売りたい」と国内でも販売されるようになり、売れ始めました。
◆ 決定的な差別化を図るため、世界初の「レール交換方式」を開発
― 「ネジのばらつきが大きい海外でも使える装置を」というニーズに応えたことで、海外で貴社の自動ネジ供給機が売れたことは想像できますが、ネジのばらつきが少ない日本においても、貴社のネジ供給機が国内シェア1位になるほどまで売れた理由は何ですか?
当時の自動ネジ供給機は、日系大手電機メーカー1社による独占市場だったので、お客様からの「こうしてほしい」という細かなニーズに応えてはいませんでした。我々は中小企業で小回りが効きますので、すべてのクレームに応えて改良を続けました。実は今でも外からは見えないところで常に改良が入っており、製品の部品や材質等も進化し続けています。
― どのようなクレームに応えたのですか?
当時の既存品はネジをフォークですくいあげ、自重で落下させる方式だったため、ネジが詰まりやすく、扱えるネジのサイズも限られていました。特に近年、製品組立ラインもロボット化が進んでいますので、ネジ詰まりで分単位でもラインが止まってしまうと生産性が落ち、大きなダメージになります。そこで、これらの問題を解決するため、モーターの振動でレール上のネジを整理し水平に搬送する新しい方式を考えました。さらに、そのレールの特徴を最大限に活かして従来品との決定的な差別化を図るため、世界で初めてレール交換方式を考案しました。従来品はネジの種類が変わるたびに装置自体を買い換える必要がありましたが、オプションのレールを交換するだけで、多様なサイズや形状、材質はもちろん、多くの特殊ネジにも対応できるようにしたのです。
モーターの振動でネジを水平搬送させる新しい方式を開発し、さらに世界で初めて「レール交換方式」(特許取得)を採用した同社の自動ネジ供給機(動画)。
7種類あった装置を1台にまとめた分だけ、当社の売上は落ちたなと思いましたけど(笑)。お客様にとって何がベストかと言えば、レールだけ交換できた方がコストも安く済みますし、生産ライン変更にもすぐ対応することができます。"私どもにとってのベスト"ではなく、"お客様にとってのベスト"を選んだ結果、お客様からは喜んでいただけました。一度購入してくれたお客様は必ずリピートしてくれます。また、機構がシンプルなので修理がしやすいという特長もあり、10年以上経った製品の修理を依頼されるお客様もいます。当社としては修理よりも新しい装置を購入いただいた方が売上は上がりますけど(笑)。お客様側で最適にカスタマイズできる余地を持つ製品を開発したことが、お客様から評価いただいた一番の要因になったと思います。はじめ競合他社からは「たいしたことがない」と言われたのですが、最後にはそれが当社の一番の特長になりました。一時期は「もし世の中がネジ不要になったらどうしよう」と心配したこともありましたが、そんな世界にならず安心しています(笑)。
― それほど画期的な装置を、他の企業は真似できないのでしょうか?
1996年の販売以来、常に改良を繰り返して少しずつ製品のラインナップも増やしており、お客様からの多様なニーズに応えるため、50以上のバリエーションを取り揃えています。品質的に同等以上の製品をつくることも、また、これだけのバリエーションを揃えるのも、難しいのではないでしょうか。
一方、最近は中国等の海外で当社製品の模倣品が大量に出回っており、その対策に頭を悩ませています。模倣品も年々精巧になっており、デザインのみならず、商標ラベルまでコピーされてしまい、外見を見ただけでは本物との区別がつかないほどです。酷いものは装置の一部だけが偽物になっており、使用中に不備が出て、偽物と気づくケースもあります。いたちごっこではありますが、お客様からも「安定性の高い本物を探し求めている」と聞くので、ブランド戦略の見直しや製品ラインナップの充実化等による模倣品対策を進めています。
◆ 技術力の高い開発型メーカーとして認められる
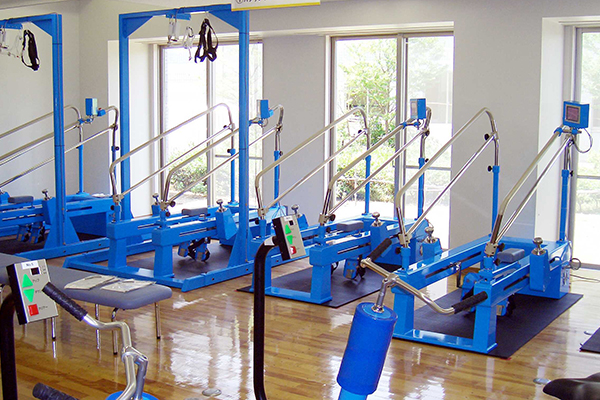
認知動作型トレーニングマシン
― 現在はどのような事業を展開していますか?今後の展望についても教えてください。
最近は異業種の大手企業からお声がけいただき、協働事業が増えています。ひとつは自動車産業で、大手自動車工場に当社の装置を組み入れていただいたり、大手ロボットメーカーとのタイアップで次世代型ロボットリハビリテーションシステムを開発中です。東京大学の小林寛道先生が開発した認知動作型トレーニングマシンの製造を行うことも決まり、研究用機器から販売製品への展開を目指しています。健康志向の高まりや高齢化社会の進展に伴い、当社のトレッドミルが開拓できる新市場はまだまだあると考えています。
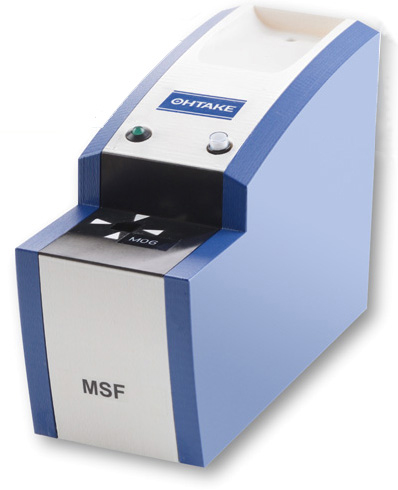
マイクロネジ供給機
自動ネジ供給機分野においても新たな市場の開拓を進めており、ウェアラブル機器の新市場を狙って微細なネジ(直径0.5mm)用の新製品「マイクロネジ供給機」を東北大学超低摩擦技術領域との連携で開発しました。このほかにもIoT化への対応等、製品に「完成」というものはなく、やらなければいけないことはたくさんあると考えています。
昔の下請けだった時の仕事と、今の仕事は全然違います。取引先は大企業ですが、今は買い叩かれないどころか、我々のことを対等に扱ってくれ、メーカーとして尊重してもらっていると感じます。それは他につくれないオンリーワンの技術を我々が持っているからです。至らないところもまだまだ多いですが、他社の方が助けてくれ、周囲に恵まれていると感謝しています。
社長が二十歳だった頃
― 次に、太田さんが二十歳だった頃について教えてください。
◆ 父から「戻ってこなければ勘当だ」「金はやるからお前が全部やれ」と言われ会社設立。
外資系の仕事をしたかったので、ある外資系企業を志望したところ「面接までの一週間で全部読んで理解しなさい」と半導体に関する英語の教科書を渡されました。最初は真面目に勉強しましたが、できるはずがないですよね(笑)。今でも英語は一番苦手なんです。仕方がないので面接会場に行くと、初っ端から英語で半導体の質問をされました。「わからないです」と正直に答えると、面接官が急に日本語を話し始め、「無理なのは最初からわかっていて、この課題を出しました。あなたは逃げずに面接に来ました。それを評価します」と、その場で採用が決まりました。現地法人を立上げるために人材を集めている最中だったので、「入社まで修行してきなさい」と猶予期間が与えられました。
ところが父から「岩手に戻って来なければ勘当だ」と言われました。先程もお話した通り、バンドソーを開発したのは父で、東京の商社と契約したものの、なかなか売れずにいました。そんな中、件の大手電動工具メーカーからOEMの依頼があった時、父は契約した会社との関係で、そのメーカーとの契約ができなかったので、新しい社長で会社を立ち上げる必要があったのです。父からは「金もやるから、名前も会社登記も全部お前がやりなさい。お前に全部任せた」と丸投げされました。そのために、若い頃はだいぶ苦労しました。設立当時はまだ24歳で、世間知らずだったこともあって、取引先からは「ぼっちゃん」と呼ばれたりしていました。
― 外資系企業に就職するつもりが、急に「会社を設立しろ。全部任せた」と言われた当時のお気持ちは?
何千万円という大金をぽんと渡されて、萎縮してしまいました。だって、学生だったもの。大変でしたよ。何とも仕方ないですけどね。ただ、技術面では父のサポートがありました。父も製造業をやっていた影響か、私も小さな頃からモノづくりが好きでした。小さな頃は、工場で遊んでいた時、「絶対に触るなよ」と父から言われたものを、こっそり触って、よく怪我をして、よく叱られていました。中学校の頃は、巨大ロケット花火をつくろうとして、火薬を集めて試したら、大爆発しました。爆発音で周囲にいた子どもの耳も一時的に聞こえなくなるほどの大爆発でした。幸い他の生徒に怪我人はいませんでしたが、今も私の片目が見えづらく指も1本ないのは、その時の怪我です。学校の先生からは「我が校始まって以来の大惨事だ。君は将来、発明家になりなさい」と言われました。
― 非常にインパクトのあるエピソードから、太田さんのモノづくり力や実行力のルーツを感じられた気がしました。
我が社の環境自慢
― 続けて、貴社の環境自慢を教えてください。
◆ 小さくともメーカーであること
部品ではなく、自分たちで考えたモノを完成品として世の中に売る、小さくともメーカーであることです。
◆ 世界に通用する製品をつくる
地方にある中小企業ながら、世界中にモノを売っており、世界中から問い合わせが来ることです。
◆ 大学や研究機関等との協働で、新たな付加価値を創造できる
研究開発に力を入れており、大学や研究機関等、異業種とも協働しながら、次代の新しいモノを創る環境があることです。
◆ ビジネス的にポテンシャルの高い位置にいる
私としての一番の自慢は、周囲の人たちから「売れるモノを持っている」と思ってもらえる環境があることです。市場規模が1兆円を超え、今後さらなる発展が見込める健康福祉産業に我々が売れるモノはたくさんあると可能性を感じています。やれることは、まだまだたくさんあるのです。
次世代へのメッセージ
― 最後に、今までのお話を踏まえて、若い世代にメッセージをお願いします。
◆ まずはやってみたらいいじゃない
やりたいことがあるなら、頭で考えるのではなく、まずは自分でやってみるといいですよ。だって、やってみないとわからないじゃない。1回やってみて、もし駄目だったら、じゃあ、どうしたらできるのかを突き詰めて考えればよいのです。私はよく社員や娘にも言いますが、私が聞きたいのは、できない理由ではなく、どうやったらできるかなんです。もし駄目でも、別に命までとられるわけではないのだから、失敗を恐れず、ぜひ挑戦してください。
― 太田さんのスタンスがよく伝わってくるメッセージだと感じました。太田さん、本日はどうもありがとうございました。
社員に聞く、我が社の環境自慢
◆ 完成品の設計・開発から生産・販売まで手掛けられるメーカー
/佐藤大介さん(35歳、入社2年目、岩手県一関市出身)
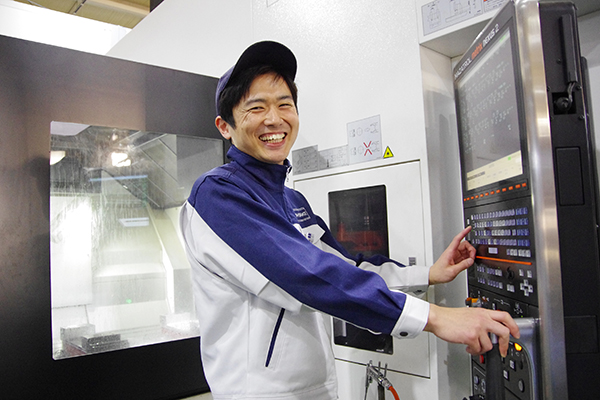
もともと東京で仕事をしていたのですが、家庭の事情で岩手に戻ることになり、ハローワークから紹介された1社目の企業が当社でした。前職の加工の経験が活かせると思い、迷わず当社を志望し、無事採用いただいて今年で入社2年目です。現在、私の入社と同時期に新設された製造技術部で、設計と加工の現場の人たちをつなぐパイプ役を担っています。例えば、設計図面をどの機械でどのように加工するかを現場の人たちと相談したりしています。
我が社の環境自慢は、独自技術で、完成品の設計・開発から生産・販売まで、トータルで手掛けることができるメーカーであることです。岩手の特に中小企業では、そのようなメーカーは非常に少ないので、入社してからそれを知って驚きました。開発から生産まで全てを当社で行うため、全体を把握することができますし、工場内には様々な機械が揃っています。今まで触ったことのない色々な機械を使えること自体がおもしろいですし、社員のスキルアップ面でもよい環境です。製造技術部のミッションである現場の改善に今後も積極的に取組み、社員の一人としてよりよいモノづくりを目指していきたいです。
コラボレーション
おすすめ記事
![]() |
【特集】宮城の研究施設 一般公開特集 |
![]() |
【特集】仙台市総合計画審議会 仙台の10年をつくる |
【社会】社会って、そもそもなんだろう?

青井真さん(防災科学技術研究所)に聞く:<東日本大震災から10年>東北地方太平洋沖地震が起きて、地震研究はどう変わった? 2021.11.11 【大草 芳江|社会って、そもそもなんだろう?|科学って、そもそもなんだろう?|防災科学技術研究所】

前田拓人さん(弘前大学)に聞く:<東日本大震災から10年>もし東北地方太平洋沖地震が起きていなければ、地震研究はどうなっていた? 2021.10.08 【大草 芳江|弘前大学|社会って、そもそもなんだろう?|科学って、そもそもなんだろう?】

日野亮太さん(東北大学)に聞く:<東日本大震災から10年>もし東北地方太平洋沖地震が起きていなければ、地震研究はどうなっていた? 2021.10.02 【大草 芳江|東北大学|社会って、そもそもなんだろう?|科学って、そもそもなんだろう?】
同じ取材先の記事
◆ 大武・ルート工業

【オンリーワン企業がオンリーワンたる所以を探る Vol.17】「まずはやってみる」の開発力で、世界中が使いやすい製品を追求し、トレッドミルと自動ネジ供給機でオンリーワン/大武・ルート工業(岩手県一関市)社長の太田義武さんに聞く 2018.04.09 【大草 芳江|公益財団法人東北活性化研究センター『”キラリ”東北・新潟のオンリーワン企業』Collaboration連載企画|大武・ルート工業|社会って、そもそもなんだろう?】
社会って、そもそもなんだろう?
最新5件
カテゴリ
取材先一覧
■ 幼・小・中学校
■ 高校
- ・仙台一高 (15)
- ・仙台二華 (14)
- ・仙台二高 (12)
- ・仙台城南高校 (5)
- ・仙台城南高等学校 (0)
- ・仙台高専 (4)
- ・宮城一高 (4)
- ・宮城県高等学校理科研究会 (2)
- ・岩ケ崎高 (1)
- ・東北工業大学高校 (0)
■ 大学
■ 国・独立行政法人
- ・内閣府 (1)
- ・宇宙航空研究開発機構 (5)
- ・文部科学省 (0)
- ・東北経済産業局 (17)
- ・水産総合研究センター東北区水産研究所 (1)
- ・理化学研究所 (3)
- ・産業技術総合研究所東北センター (36)
- ・科学技術振興機構 (1)
- ・防災科学技術研究所 (1)
- ・高エネルギー加速器研究機構 (1)
■ 自治体
- ・仙台市 (8)
- ・仙台市博物館 (4)
- ・仙台市天文台 (12)
- ・仙台市教育委員会 (13)
- ・仙台市産業振興事業団 (1)
- ・仙台市科学館 (8)
- ・仙台文学館 (2)
- ・仙台管区気象台 (2)
- ・塩釜市 (3)
- ・宮城県 (8)
- ・宮城県古川農業試験場 (2)
- ・宮城県教育委員会 (1)
- ・宮城県農業・園芸総合研究所 (1)
- ・気仙沼市 (1)
- ・登米市 (1)
■ 一般企業・団体
- ・DIC株式会社 (2)
- ・K sound design (1)
- ・KDDI (2)
- ・natural science (1)
- ・せんだい・みやぎNPOセンター (2)
- ・てとてと (1)
- ・ひのき進学教室 (11)
- ・みやぎ工業会 (8)
- ・みやぎ工業会会長 (0)
- ・みやぎ産業振興機構 (3)
- ・アスター (1)
- ・インスペック (1)
- ・エツキ (1)
- ・ソニー (3)
- ・ソニー教育財団 (1)
- ・ソフトバンク (1)
- ・ティ・ディ・シー (1)
- ・デュナミス (1)
- ・ドットジェイピー (1)
- ・ナノテム (1)
- ・ハリウコミュニケーションズ (3)
- ・ハード工業有限会社 (1)
- ・フジイコーポレーション (1)
- ・プレファクト株式会社 (1)
- ・ヤマダフーズ (1)
- ・全国学習塾協会 (3)
- ・公益社団法人セーブ・ザ・チルドレン・ジャパン (1)
- ・勝山酒造部 (1)
- ・及源鋳造株式会社 (1)
- ・大武・ルート工業 (1)
- ・太白少年少女発明クラブ (1)
- ・宮城の新聞 (0)
- ・宮城県中小企業家同友会 (1)
- ・宮城県産業人クラブ (0)
- ・宮城県職業能力開発協会 (1)
- ・宮城県酒造組合 (2)
- ・工藤電機 (2)
- ・平孝酒造 (1)
- ・応用物理学会 (2)
- ・新東総業株式会社 (1)
- ・日刊工業新聞社 (7)
- ・日本アンドロイドの会 (1)
- ・日本技術士会 (2)
- ・日本私立大学団体連合会 (1)
- ・日本農芸化学会東北支部 (1)
- ・日本IBM (3)
- ・日東イシダ (1)
- ・有限会社 柏崎青果 (1)
- ・東京エレクトロン宮城 (1)
- ・東北ニュービジネス協議会 (1)
- ・東北活性化研究センター (3)
- ・東北経済連合会 (1)
- ・東北電力 (2)
- ・東北電子産業株式会社 (1)
- ・東栄科学産業 (1)
- ・林精器製造 (1)
- ・株式会社三栄機械 (1)
- ・株式会社悠心 (1)
- ・河北新報 (1)
- ・神田産業株式会社 (1)
- ・秋田化学工業 (1)
- ・笹氣出版印刷 (1)
- ・米鶴酒造 (1)
- ・萩野酒造 (1)
- ・農芸化学会 (1)
- ・遠藤工業 (1)
- ・鈴木製作所 (1)
- ・阿部蒲鉾 (1)
- ・阿部蒲鉾店 (1)
- ・鳴子の米プロジェクト (1)
- ・NECトーキン (1)
特別企画 「宮城の塾」
![]() |
学習塾から見る 宮城の教育の「今」 塾選びに一役 |

![]() |
【科学って、そもそもなんだろう?】 若手研究者座談会「地震学×情報科学の融合で得られたもの」 2024.09.16 |
![]() |
【科学って、そもそもなんだろう?】 地震の発生予測に挑む(京大防災研の西村卓也さん・京大名誉教授の平原和朗さんに聞く) 2023.01.26 |
![]() |
【社会って、そもそもなんだろう?】 【同窓生に聞く#01】中鉢良治さん(元ソニー社長、産総研最高顧問)がリアルに感じていることって、何ですか? 2022.10.27 |
![]() |
【科学って、そもそもなんだろう?】 地震学×情報科学の融合で、目指すは天気予報の地震版 2022.04.13 |
![]() |
【社会って、そもそもなんだろう?】 「仙台の地形と水との関わり」~地形から見る仙台の過去・現在・未来~ 2022.03.02 |
![]() |
【科学って、そもそもなんだろう?】 青井真さん(防災科学技術研究所)に聞く:<東日本大震災から10年>東北地方太平洋沖地震が起きて、地震研究はどう変わった? 2021.11.11 |
記者ブログ
![]() |
ひとり新聞社「宮城の新聞」の大草よしえが衆院選に立候補 2021.10.19 |
![]() |
最近の活動は「Twitter」に移行しました 2019.11.01 |
![]() |
【追記】テレビ朝日「モーニングバード」スタジオ生出演&iCAN'15世界大会(アラスカ)世界第1位! 2015.06.19 |
![]() |
2014年の振り返りと、2015年の抱負 2015.01.05 |
![]() |
平成25年度を振り返りました・・・。 2014.04.02 |
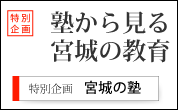
![]() |
中野塾(泉中央・北高森) |
![]() |
ひのき進学教室(泉中央・長命ヶ丘・八幡教室・上杉教室) |
![]() |
夢学館(東照宮・福室) |
![]() |
早稲田育英ゼミナール(泉中央) |
![]() |
ソーメック個別学習院(若林区、太白区、泉区に6教室) |
![]() |
明和塾(北山・八木山) |
![]() |
JUKU ペガサス仙台南光台教室(南光台南) |
アクセスランキング
- 【宮城の塾】 宮城の塾 仙台市を中心とした学習塾・幼児教室・進学塾の特集
- 世界中の研究者が憧れる研究拠点へ/東北大学WPI-AIMR本館竣工記念式典/科学って、そもそもなんだろう?
- [vol.1] 第1回宮城の日本酒を楽しむ会/社会って、そもそもなんだろう?
- 「仙台の地形と水との関わり」~地形から見る仙台の過去・現在・未来~/社会って、そもそもなんだろう?
- 宮城県仙台第一高等学校/教育って、そもそもなんだろう?
- 【宮城の塾】 ひのき進学教室(泉中央本部教室・八幡町教室・上杉教室・五橋教室・長町教室・愛子教室・吉成教室・大和町教室、他)
- 地震の発生予測に挑む(京大防災研の西村卓也さん・京大名誉教授の平原和朗さんに聞く)/科学って、そもそもなんだろう?
- 【宮城の塾】 JUKU ペガサス仙台南光台教室
- 【宮城の塾】 質問できます!/宮城の塾|宮城の新聞
- 【宮城の塾】 明和塾(北山教室・八木山教室)