取材・写真・文/大草芳江
2018年02月15日公開
高級腕時計ケースの「美しいものづくり」を
ベースに事業を多角化。
最終目的は「いいものをつくる」こと。
林精器製造株式会社(福島県須賀川市)
代表取締役社長 林 明博 Akihiro Hayashi
公益財団法人東北活性化研究センター『"キラリ"東北・新潟のオンリーワン企業』Collaboration連載企画 (Vol.09)
福島県須賀川市に本社を構える林精器製造株式会社(1921年設立、従業員323名、資本金9,000万円)は、精密金属加工と美しいものづくりの融合を顧客価値として提供する、国内唯一の腕時計ケース専業メーカーである。現在、創業事業である腕時計ケース製造を軸に、ロボット装置・ファクトリーオートメーション機器の設計・製造、装飾・機能めっきの受託処理等を県内3つの事業所で行っている。2011年に発生した東日本大震災では本社須賀川工場の約7割が使用不能になる大きな被害を受けたが、数多くの方々の支援と社員の奮闘により比較的早期に復旧できた。2013年には新築となった工場への帰還を果たし、新たな成長に備えている。2012年「第4回ものづくり大賞」特別賞受賞、2014年「がんばる中小企業・小規模事業者300社」認定。そんなオンリーワン企業の林精器製造がオンリーワンたる所以を探るべく、代表取締役社長の林明博さんに話を聞いた。
オンリーワン企業になるまでの軌跡
― はじめに、貴社がオンリーワン企業と言われる所以を教えてください。
実を申し上げますと、当社は本当の意味でのオンリーワン企業です。日本国内に腕時計ケースの専業メーカーは今や当社一社しか残っていません。創業96年以来、当社が唯一一貫して取り組んできたのが時計ケースの製造です。現在、国内大手時計メーカー3社のうち、2社と取り引きしています。当社以外で時計ケースを製造しているところはどこにあるかというと、時計メーカー内部の仕事として位置づけられています。それくらい時計ケースは腕時計において重要な要素を占めると言えます。
96年の社歴の中で、時代の変遷もあり多くの災害もありました。とりわけ大きな転換点が太平洋戦争の勃発です。当時は東京に本社工場がありましたが、戦火の拡大とともに徐々に軍事工場化し、時計ケースの製造が事実上できなくなりました。「このままでは生産再開は望めなくなる可能性がある。主要な生産設備だけは別の場所に移したい」との想いを当時の経営者が持ち、その移転先がここ福島県須賀川市でした。1943年に生産拠点を移してから今日に至るまで、須賀川市が私どもの本拠地になっています。当時東京にあった工場は、1945年の終戦を迎える前に戦火に落ちてしまいました。もし生産拠点を移していなければ、当社の歴史はそこで途絶えてしまった可能性は十分に考えられるでしょう。
その後、1980年から1985年頃にかけて、当社における製造のピークを迎えます。正直に申し上げますと、この時代のお客様はただ1社でした。その1社の時計メーカーに対して当社が時計ケースを供給し、その生産量は月50万個、年間にして630万個という記録が残っています。ところが1985年から1990年代に至るや、多くの工業製品の生産拠点が日本国内から人件費の安い海外へシフトしました。この流れは時計ケースも同様でありまして、年産630万個をピークとし、年を追うごとに生産量は減少しました。そんな中で当社は、最上位モデルの時計ケースのみに特化し、さらに他事業にも多角化展開を図ることで、今日まで生き延びることができたのです。
今日の当社の姿は、ここ須賀川事業所において時計ケースを製造する他にも、さらに二つの機軸事業領域があります。ひとつは玉川事業所のメカトロ事業部で機械装置の設計製作を行い、ロボットやファクトリーオートメーション関係の事業を手掛けています。もうひとつの郡山事業所では、めっき表面処理事業を行っています。この3つの事業体制ができあがったのが、2000年の段階でした。
そこで、冒頭に申し上げた当社が「オンリーワン企業」になった経緯についてですが、1985年をピークに、時計ケース製造のうち、とりわけ低価格品の生産が海外に流れました。それに伴い、大手時計メーカーに供給していた時計ケースメーカーの仕事量は減少し、廃業や転業、もしくは大手メーカーと一緒に海外へ生産拠点を移す動きとなりました。その結果、ある大手時計メーカーに対して当時25社程存在していた時計ケース専業メーカーの中で、日本国内で今も事業として継続しているのは当社1社のみになった次第です。
◆ 日本国内に1社だけ残った理由
― なぜ貴社1社だけが存続できたのでしょうか?
当社が今日まで生き残れた要因のひとつは企業の規模で、当社が最大でした。ふたつ目は圧倒的な技術力の差だと思います。技術とはお客様との信頼関係そのものです。ちなみに、高級時計のパンフレットでよく見られる「ザラツ研磨」という言葉自体は当社の発祥です。もともとスイスで使われていた先進的な研磨加工技術を当時の社長が何とか導入したいと現地調査等を行い、それが「ザラツ」という会社の機械であることがわかりました。そこで、ザラツ社の機械を導入し、その技術を定着させたのです。以来、その研磨技術については、「ザラツ研磨」という言葉が、業界用語ではありますが一般名称となっています。
加えて事業の多角化展開を図れたことも当社の経営安定化に大きく寄与したと思います。現在、当社のビジネス全体に占める時計ケース売上の割合は約45%で、残りの約55%はそれ以外のビジネスが占めています。めっき表面処理も機械装置の設計製作も、もともと当社内の時計ケース製造というビジネスエリアに付随していた一工程でした。それから約20年が経った今、事業内容は大きく変化しており、当社の本業である時計ケースとは全く異なる内容仕事になっています。
◆ 時代の流れにうまく適応して生き残る
― めっき表面処理と機械装置の設計製作、それぞれどのようにして時計ケース製造の一工程から事業の多角化を図れたのですか?
まず、めっき表面処理事業についてお話します。時計ケースの材料には、もともとチタンやステンレスなどの錆びにくい高級な材料が使用されていますが、かつての月産50万個の時代には、いわゆる黄銅や洋白といった、錆び易い合金が使われていました。そのため当時の時計製造には、めっき表面処理が必要な技術でした。そこで、以前から付き合いのあった、めっき会社を当社のグループの中に招き入れた次第です。その後、めっきが必要な低・中価格帯の時計ケースの生産がすべて海外へ移り、日本国内での生産がほぼなくなりました。そこで、他に事業展開ができないかを考えました。
めっきには、大きく分けると2種類あります。色や質感の改善など外観の美観を与える「装飾めっき」と、めっき皮膜そのものの特性を利用して、電気伝導性などの機能を与える「機能めっき」です。当社はずっと装飾めっきを専門としてきましたが、装飾めっき分野は先細りであろうとの見通しを受けて、機能めっきに"業種転換"したのです。これは"業種転換"というほど大きな変化で、苦労に苦労を重ねて、機能めっきにシフトしました。
そこで始めたのが、フレシキブル基板という、回路基板のパターンをめっきでつくる技術の開発です。実はこれが"大当たり"しましてね。ちょうど2000年から2010年頃までが、携帯電話の爆発的な普及期を迎えた頃でしたので、折りたたみ式の携帯電話に必ず1台に1枚ずつ使われるフレシキブル基板の需要が爆発的に増えたのです。当社においても装飾めっきから機能めっきに切り替えたちょうどその後、フレキシブル基板の爆発的ブームが到来し、そういう意味では、非常に助かりました。お客様からの増産要請に応えるのは非常に苦しい面もありましたが、めっき事業をうまく時代の流れに乗せることができました。
では今はどうなっているかと言うと、それから10年経った今、フレキシブル基板のビジネスは0です。グローバル化に伴い、日本国内でフレキシブル基板を製造しているメーカーはほとんどなくなりました。それだけ時代の移り変わりが激しい事業なのです。ちょうどフレシキブル基板の製造が危ないなと思っていたところに、次段階で増えてきたニーズが、装飾性の高いプラスチック製品に対して金属感を与える装飾めっきでした。そこで当社は装飾めっきの方にまた戻ったわけであります。現在では表面処理事業の売上の約85%が、プラスチックの射出成形品に対するめっき処理です。
― 時代のニーズの移り変わりの激しさを貴社の歴史から感じますね。
そうですね。終始一貫変わっていないのは時計ケースの事業だけで、その他の事業は本当に大きく変化しています。時代の変化に追従できたからこそ、生き残っているのです。
◆ リーマンショックという逆境の中で見直した事業価値
もうひとつの機械装置の設計製作については、世の中が大量生産から多品種少量生産へシフトする中、社内で専用機械を製造する必要性がなくなったため、この部門を独立させて社外向けの対応を行おうとスタートを切りました。機械装置の設計製作も今では約98%が社外のお客様向けです。
この事業も大きな浮き沈みがありました。一時期は大手家電メーカーのOEM生産を手掛けるなどして凌いできましたが、一番の大きな変化がリーマンショックでした。これから本格的な拡大期を迎えるということで、半導体製造装置の開発をあるメーカー様と一緒に進めており、当社としてもクリーンルームを設ける等、莫大な設備投資を行っていました。しかし、クリーンルームの開所式まで実施した矢先にリーマンショックが起こり、その仕事は完全になくなってしまったのです。それが当社の機械装置部門の一番苦しかった時期で、リーマンショック前と直後で、部門売上はなんと10分の1まで落ち込んでしまいました。そこからの再スタートとなったわけでありますが、当社の事業の価値はどこにあるのかを、よく考え直し、実に色々なことをやりました。
― 貴社が提供できる価値をどのように見直したのですか?
我々が提供できるのはあくまでソリューションであるという原点に戻りまして、お客様のニーズに合わせたファクトリーオートメーション機器・ロボット装置のソリューションビジネスを展開しました。現在はさらに世の中が進んでいますので、よりシステマティックな内容へシフトしています。ただ、ソリューションビジネス1本だけでいくには当社の規模はやや中途半端でして、経営的な安定性を高めるためには、部品加工という新たな領域が、機械装置の設計製造を支える構造として必要だと考えました。そこで現在、医療機器や航空機、次世代自動車の部品加工といった、次代を担う新規分野の開拓も積極的に進めています。
◆ 「美しいものづくり」のDNAで高付加価値産業を狙う
― 部品加工という新たな事業領域において、もともと貴社が持っているどのような強みが活かされますか?
お客様からはよく「非常に仕事が丁寧ですね」と仰っていただきます。これは当社のDNA的なものが多分に影響していると思うのですが、メカトロ事業部に現在所属している従業員たちのルーツを辿ると、時計ケースの製造から入っています。時計ケースは外観的な「美しさ」が命の製品ですので、自然と物の扱い方や加工面の出来栄え等が一般的な加工屋さんとは違ってくるのでしょう。お客様が手にとって見ていただくとおわかりになっていただける丁寧さが、製品に現れるのだと思います。ただ、必ずしも丁寧だからよいというわけではありません。丁寧というのは多分にコストがかかります。「丁寧だけど、高いね」と同じタイミングで言われるお客様もいらっしゃるので、それが悩みでもありますね。
― そこで、もともとの値段が高くて丁寧さが求められる分野として、医療機器や航空機、次世代自動車などの高付加価値製品にターゲットを絞っているのですね。
仰る通りで、もうその分野しかないと思っています(笑)。当社がボルトや金具のような同一部品を大量に生産することはとてもできません。これまで私どもが時計ケース製造で生き残ったように、将来的には医療機器や航空機、次世代自動車にしましても、小ロットで高付加価値な製品分野を狙っていくのがよいと考えています。
◆ 東日本大震災で本社工場全壊 社員一丸となっての早期復旧
― 2011年3月11日に発生した東日本大震災では、貴社須賀川工場の約7割が使用不能になるという甚大な被害を受けました。
当社の96年の社歴の中におきましても、関東大震災と太平洋戦争敗戦と東日本大震災、この3つは語るに避けて通れない出来事だと思います。東日本大震災では、ここ須賀川は最も激しく揺れた場所のひとつでして、当社の鉄筋コンクリート3階建ての建物が見るも無残に倒壊しました。倒壊した3階には当時、約50名の社員がいましたが、重傷者は一人もなく、この事態を切り抜けられたことは大変有り難いことでした。2年後の2013年2月、幸いにしましてグループ補助金で、現在の社屋をこの場所に再建築し、もとの仕事ができるようになりましたが、今日に至るまでは本当に大変でした。その中でも一番苦しかった時期が震災発生からの3年間です。
震災発生直後は、一刻も早い生産再開にむけて、まず生産再開をどこでどのようにするか、すぐに動き出しました。当社が部品を製造できなければ、その先にある製品も生まれません。製造業を営む以上、ものづくりのつながりを途切れさせることは許されないのです。幸いにしまして、震災発生から2週間以内の早い段階で、生産再開の場所は決まりました。偶然、お客様が須賀川市内に遊休工場を所有していることを知り、何とか貸してもらえないかと、直ちに出向いてお願いしたところ、二つ返事で借り受けることができたのです。
場所は決まりましたが、生産再開にあたっては、当然ながら機械装置を移動させなければなりません。ところが装置は倒壊した建物の中にありましたので、失ったものは除いても300台以上もある装置を倒壊した建物から引っ張り出してトラックに乗せて運び、仮工場に設置して稼動させる作業を行う必要がありました。まず運送業者に相談しましたが、どこに相談しても引き受け手がいませんでした。その理由は、現実的に資材も人手も集まらないし、あまりにも作業現場が危険だからということでした。そこでいよいよ「もう自分たちの力で移設せざるを得ない」と心を決めまして、約35人を選抜して3班つくりました。第1班は倒壊した建物の中から使える機械装置を引っ張り出し、第2班はそれをトラックに乗せて新しい仮工場へ運び、第3班は仮工場に設置した機械の動作確認をして立ち上げました。必死に作業を続けた結果、震災から約3週間で約300台の機械を仮工場に設置することができ、一部を除き、製造ラインを再開することができたのです。
「生産再開は震災発生から3ヶ月」という目標を立てていました。実は当初、5ヶ月程度はかかるだろうと見ていたのですが、5ヶ月も経ってしまうと仕事を戻せないことがわかり、何としても3ヶ月で生産再開せざるを得なかったのです。約300台の機械には修理が必要なものも多くありました。これもできる限り自分たちで修理を行いました。結果として、2011年6月6日、目標通り、震災発生から3ヶ月で全工程の生産再開を果たすことができました。
◆ 震災で約3割の仕事を失うも、業績回復できた理由
しかしながら、当社の売上の約55%のビジネス領域を担う須賀川事業所が約3ヶ月間、生産停止した影響は、決して小さくはありませんでした。震災から3ヶ月後に生産再開を果たしたものの、やはり仕事の多くは失われてしまったのです。実は震災の瞬間にはっきりと無くなってしまった仕事が2種類ありました。ひとつはサプライチェーンに乗っていた仕事です。震災が発生した翌々日にはもう仕掛品(製造途中にある製品のことで、そのままでは販売できないもの)の引き取りに来ました。サプライチェーンが一旦途切れてしまうと、全体の生産に影響が出ますから、その影響を最小限に食い止めるために、サプライチェーンの寸断された部分が直ちに補修されます。そのため仕掛品の引き上げが必要になってくるわけです。サプライチェーンが一旦補修されてしまえば、我々はもう二度と戻ることができません。もうひとつは海外のビジネスを、その瞬間にすべて失いました。特に東電福島第一原発事故に伴う風評被害の影響は大きなものでした。これらによって失った仕事は、全体の約3割でした。
一度失った仕事は二度と戻ってきません。失った仕事を別の何かで埋めるか、もしくは、事業縮小化か、その二者択一を迫られました。当社の場合、何とか事業縮小化はせず再生を図りたいということで、その分、社員一人ひとりには説明をした上で、非常に大きな苦労をかけました。それが、震災から3年間の非常に苦しかった時期のことです。その後、震災によって失われた仕事を埋める手段等々含めて回復の兆しが見え始め、今期に至っては、震災前のみならずリーマンショック前まで業績を回復することができました。
― 震災前のみならずリーマンショック前まで業績を回復できた要因とは何ですか?
ある意味、幸運もあります。現在、日本全体として好調なメカトロのビジネスが、大きく伸びてくれました。また、めっき表面処理に関しましても、プラスチックへの装飾めっきの需要が非常に大きく伸びています。さらに、本業である時計ケース製造におきましては大変有り難いことに、「一時期は転注せざるを得ないが、林精器製造がきちんとものをつくれるようになったら、必ず仕事を戻そう」と仰ってくださったお客様がその約束を守ってくださったのです。
― 先程「技術力とは信頼関係」と仰っていましたが、まさにそのことですね。
その通りです。この東日本大震災からの期間において、お客様との信頼関係がビジネスにおいて如何に大切かを今回改めて強く感じています。当社では現在、「いいものをつくる」を社是に掲げています。いいものをつくることによって、お客様との信頼関係が継続されると考えています。
― 貴社が96年間存続している根底には、様々な時代の変化や逆境にも適応するしなやかさに加え、確かな技術力に裏付けられた顧客との信頼関係があることが感じられました。
◆ 「いいものをつくる」熟練技能者の技能伝承と最先端加工技術の融合
― とはいえ「いいものをつくる」と口だけで言っても、なかなかつくれるものではないと思います。どのような仕組みで「いいものをつくる」ことを具現化されているのですか?
それは常に求めていることであって、一言で「こういう仕組みで、こうなっています」と言うことは非常に難しいのですが、当社では技術・技能の伝承を非常に大切にしています。
とりわけ研磨はかけがえのない技術で、当社には珠玉の技能者が数多く在籍しています。熟練した匠の技をどのように次代へ伝承すべきかを考えた結果、2006年から新たに始めた取り組みが、技能の伝承に特化した「ものづくり研修塾」で、現在は「ものづくり革新グループ」という形で本社機能として位置付けています。当社には、工場見学をきっかけに「自分も研磨をやりたい」と入社してくださる方が多いのですよ。研磨を希望する新入社員を少なくとも2年間、生産ラインから外れたチームで専任の熟練技能者が指導し、訓練した後、職場に配属します。あるいは適性がないと判断した場合には、他の仕事に配属します。
― OJT(実際の職場で実務を通して学ぶ訓練)ではなく、実際の業務から離れて2年間もトレーニングしてから現場投入とは、訓練期間を非常に長く取っていらっしゃる印象です。
2年間トレーニングして研磨の仕事ができるかと言えば、できません(笑)。半人前にもなっていないレベルです。ただ、それを従来はOJTで補っていましたが、同等のレベルに達するには4年から5年はかかりましたので、その分は、育成期間が短縮されています。一般的には10年間の経験を積んでやっと一人前の仕事ができるかというところです。熟練には時間が必要です。
― 熟練を要する研磨技術は、ロボットに置き換えることはできませんか? 必ず人間の手は必要ですか?
近年、ITやAI等の技術が進展する中、それらを活用してベテラン技能者のスキルを如何に伝承していくかは、ひとつの大きなテーマです。当社におきましてもロボットによる研磨に挑戦して今年で4年目となり、かなり実現できるようになっています。例えば、入社2年目の社員は、自分の手を使った研磨の経験はまだ1年で何もできないレベルですが、その研磨ロボットを使えば、10年クラスのベテラン技能者と同じレベルの仕事ができます。
ただし、研磨の技能者がいなくても仕事ができるようにしようとは、全く考えていません。例えば、20、30年の経験を積んだベテラン技能者の仕事のうち、その技に裏付けられた作業が本当に必要な領域は30~40%だと思います。すると残りの60~70%はロボットに置き換えられるだろうという考え方です。一方で、最後の30~40%は、20、30年の経験で培った人間の技能が必要です。お客様が時計を手に取った瞬間の感動は、ロボットにはつくることができません。そこは大切にしたいので、人もしっかり育成しているのです。
社長が二十歳だった頃
― 次に、林さんが二十歳だった頃について、教えてください。
◆ ものづくり好きで、自動車競技に没頭
二十歳の頃にどんなことを考えていたかを思い出せって、ちょっと厳しいなぁ(笑)。私が二十歳だった1969年、一番記憶に残っているのは、東大安田講堂事件ですね。けれども私自身は学生運動には全く興味がなく、自動車が大好きで、ラリー競技に没頭していました。当時は改造に対する規制がそれほど厳しくなかったので、山の中を走れるようにするための改造もしました。いや、暴走族じゃないですよ(笑)。自動車のクラブもつくりましてね。今でもそのメンバーとの交流は続いています。
― 当時、この会社を継ぐことに対しては、どのように感じていましたか?
親から「会社を継げ」という指示は全くありませんでした。私も継ごうという意思はなかったですね。けれども今から考えれば、漠然とですが、興味はあったと思います。実は私、大学の工学部を2回卒業しているのです。はじめに電気、次に機械を専攻しました。卒業後はスイスに2年間滞在し、スイスの時計産業とはどんなものかを身体で感じてきました。そして帰国後、当社に就職しました。当時の本社は東京にありましたので、東京に入社し、ここ須賀川工場に配属となりました。
― 当時、自動車競技に没頭したり、電気と機械の2分野を専攻したり、スイスに滞在したことは、今の林さんとどのようにつながっていますか?
すべてつながっていると思います。そのような意味では、二十歳の頃を考えてみると、当社に入る意志はすでに出来上がっていて、そのための準備期間だった感じがしますね。ただ、大学の専攻を電気から機械にしたのは、あまりにも電気がおもしろくなかったから(笑)。機械はよかったです。自分に合っていました。
― その後、社長に就任されるまでは、どのような流れでしたか?
1987年まで須賀川で勤めた後、1988年に一度退社し、足掛け21年間、東京で自分の会社を経営していました。そして2009年、当時は私の兄が当社の社長を務めていたのですが、年齢的に私と交代すること含みで須賀川に戻ってきました。2010年6月、当社6代目の代表取締役社長に就任し、それから1年も経たないうちに東日本大震災が発生したわけです。
― そして先程お話されていたこととつながるのですね。林さんにとって、社長に就任することは自然なことでしたか?
私にとっては比較的自然でした。もともと車が大好きなので、ものづくりに対する基本的な興味がありました。それが当社の事業とも相性がよかったのだと思います。
我が社の環境自慢
― 続けて、貴社の環境自慢を教えてください。
◆ 「いいものをつくる」ための人の技能の伝承
私にとって自慢できる当社の環境は、何と言っても人の技能の伝承です。ロボットを活用できるようにしたい面もありますが、その最終目的はロボットを使うことではなく、「いいものをつくる」ことです。「いいものをつくる」には、人の技能の伝承は絶対に必要な要件です。そのために今、当社が本社機能として位置付けているのが先程お話した「ものづくり革新グループ」での技能伝承です。指導しているベテラン技能者そして若手技能者から、ぜひ話を聞いてもらえると嬉しいです。
若者へのメッセージ
― 最後に、今までのお話を踏まえて、若い世代に対するメッセージをお願いします。
◆ どんなことでもいいから、自分で考えたことを形にしてみて
世の中がどんどん便利になり、その便利さ故、人は何も考えなくても何かができる環境になっています。若い世代で起こっているもの離れは、決して若い人たちがものに対する興味を失ったわけでなく、ただ興味の対象がピンポイントになっただけで、その頂点がスマホであろうと思うのです。しかし、自分がやりたいことをどうやったらできるかを考える前に、アプリで刹那的に物事を解決してしまうと、結果的に、自分の人生がおもしろくなくなると思います。便利なアプリは結構ですが、あくまで自分の生活を楽にする上ではよいことでも、本当に自分を豊かにするものは必ずしもスマホからだけでは得られない気がするのです。
ものをつくることは、人間のみに許された特権です。人類に与えられた最大の宝物は今後とも大切にしていただきたいですね。それを誰かがやってくれるというのでは、自分の人生ですから、あまりにも勿体無いと思います。では具体的にどうするかといえば、どんなことでもいいから、自分で考えたことを自分で形にしてみることではないでしょうか。たとえ、それが価値を生まないことであっても、まずはやってみることが大切だと思います。そして、できあがった時の感動を体験できる機会をぜひとも持っていただきたいです。
― 林さん、ありがとうございました。
社員に聞く、我が社の環境自慢
◆ 積極的な若手人材育成が自慢、研磨の技を後継者に伝えたい
/有馬正則さん(62歳、入社44年目、福島県須賀川市出身)
19歳の時に入社し、今年で44年目になります。ずっと研磨の主力部隊にいて、2017年9月から、ものづくり革新グループに異動しました。現在は、トレーナーとして若い人を育成しながら研磨作業を行っています。研磨のおもしろさは自分が思うストーリーでものをつくれることですね。反面、苦しみもありますが、その分、できた時の楽しみがあります。
トレーナーとして、一番は基本をしっかり身に付けていただける指導を心掛けています。細かいことじゃなくて、やって良いことと悪いこと、ここが一番のポイントだという点を、しっかり伝えていきたいですね。従来はひとつの工程を何年もかけて習得していましたが、今の時代は短期間で育成する必要があるので、2年間で1から最後の仕上げまでを教育する計画で進めています。中級品を一人でつくれるようになることがひとつの目標です。長年、研磨をやってきたので、教えること自体は苦になりませんが、1から教えることを作業者が飲み込んでくれるか、試行錯誤しながら指導しています。
我が社の環境自慢は、このように、若手の人材育成に積極的に取り組んでいることです。どうしても昔は見て覚えるとか、長年仕事をする中で徐々に覚えていくところがありましたが、今は覚えるまで人が続かないですし、我々の高齢化も進んでいますから、先を見据えたとてもよい取り組みだと思います。できるだけ早期に積極的な人材育成を行って若手人材を底上げし実戦投入できるよう、これまで培ってきた技術を若い世代に伝えたいです。
◆ 自己研鑽を支援する教育制度が自慢、先駆的な開発の一翼を担う誇り
/秋田真輝さん(21歳、入社3年目、福島県石川郡平田村出身)
通っていた高校のすぐ近くにあり、通学路から毎日見ていた当社はすごく身近な存在で、職場体験でもお世話になりました。就職を考えた時、真っ先に候補として挙がったのが当社で、今年で入社して3年目です。現在は、研磨作業に関わる人の手間をなるべく省いて効率化を目指すロボットの開発を担当しています。
入社して半年間は研磨の基本を習った後、丸2年、研磨ロボットを日本大学工学部(福島県郡山市)と共同開発しています。まだ完璧ではないですが7割方できて、量産品の加工が始まりました。もう少し詰めれば自動化まで展開できるようになります。有馬さんをはじめベテラン技能者の方との協働で、新しいロボットと伝統に裏付けられた匠の技を融合する職場なので、お互いにわからないことがあれば聞ける環境がよいですね。ただ、研磨作業のロボット化については、まだ誰もやったことがない先駆的な取り組みなので、自分で考えるしかありません。その分、プレッシャーや不安は大きいですが、社長も研磨グループの皆もとても期待してくれているので、期待以上の成果を出したいです。
当社に入社してから、何にでも興味を持てるようになりました。特にロボット関連は自分で調べて勉強します。それが今の開発につながると思うからです。高校の時よりも今の方が勉強していますね(笑)。我が社の環境自慢は、そのような自己研鑽を会社が率先してバックアップしてくれる教育体制です。例えば、ロボットの展示会や講習会等、自分が「行きたい」と言ったところには大抵行かせてくれ、本人の自主性を尊重してくれます。須賀川の地で、技能伝承のロボット化という先駆的な取り組みを行う会社で、若手の自分もその一翼を担える環境が一番の自慢です。
コラボレーション
おすすめ記事
![]() |
【特集】宮城の研究施設 一般公開特集 |
![]() |
【特集】仙台市総合計画審議会 仙台の10年をつくる |
【社会】社会って、そもそもなんだろう?

青井真さん(防災科学技術研究所)に聞く:<東日本大震災から10年>東北地方太平洋沖地震が起きて、地震研究はどう変わった? 2021.11.11 【大草 芳江|社会って、そもそもなんだろう?|科学って、そもそもなんだろう?|防災科学技術研究所】

前田拓人さん(弘前大学)に聞く:<東日本大震災から10年>もし東北地方太平洋沖地震が起きていなければ、地震研究はどうなっていた? 2021.10.08 【大草 芳江|弘前大学|社会って、そもそもなんだろう?|科学って、そもそもなんだろう?】

日野亮太さん(東北大学)に聞く:<東日本大震災から10年>もし東北地方太平洋沖地震が起きていなければ、地震研究はどうなっていた? 2021.10.02 【大草 芳江|東北大学|社会って、そもそもなんだろう?|科学って、そもそもなんだろう?】
同じ取材先の記事
◆ 林精器製造

【オンリーワン企業がオンリーワンたる所以を探る Vol.09】高級腕時計ケースの「美しいものづくり」をベースに事業を多角化。最終目的は「いいものをつくる」こと。/林精器製造(福島県須賀川市)社長の林明博さんに聞く 2018.02.14 【大草 芳江|公益財団法人東北活性化研究センター『”キラリ”東北・新潟のオンリーワン企業』Collaboration連載企画|林精器製造|社会って、そもそもなんだろう?】
社会って、そもそもなんだろう?
最新5件
カテゴリ
取材先一覧
■ 幼・小・中学校
■ 高校
- ・仙台一高 (15)
- ・仙台二華 (14)
- ・仙台二高 (12)
- ・仙台城南高校 (5)
- ・仙台城南高等学校 (0)
- ・仙台高専 (4)
- ・宮城一高 (4)
- ・宮城県高等学校理科研究会 (2)
- ・岩ケ崎高 (1)
- ・東北工業大学高校 (0)
■ 大学
■ 国・独立行政法人
- ・内閣府 (1)
- ・宇宙航空研究開発機構 (5)
- ・文部科学省 (0)
- ・東北経済産業局 (17)
- ・水産総合研究センター東北区水産研究所 (1)
- ・理化学研究所 (3)
- ・産業技術総合研究所東北センター (36)
- ・科学技術振興機構 (1)
- ・防災科学技術研究所 (1)
- ・高エネルギー加速器研究機構 (1)
■ 自治体
- ・仙台市 (8)
- ・仙台市博物館 (4)
- ・仙台市天文台 (12)
- ・仙台市教育委員会 (13)
- ・仙台市産業振興事業団 (1)
- ・仙台市科学館 (8)
- ・仙台文学館 (2)
- ・仙台管区気象台 (2)
- ・塩釜市 (3)
- ・宮城県 (8)
- ・宮城県古川農業試験場 (2)
- ・宮城県教育委員会 (1)
- ・宮城県農業・園芸総合研究所 (1)
- ・気仙沼市 (1)
- ・登米市 (1)
■ 一般企業・団体
- ・DIC株式会社 (2)
- ・K sound design (1)
- ・KDDI (2)
- ・natural science (1)
- ・せんだい・みやぎNPOセンター (2)
- ・てとてと (1)
- ・ひのき進学教室 (11)
- ・みやぎ工業会 (8)
- ・みやぎ工業会会長 (0)
- ・みやぎ産業振興機構 (3)
- ・アスター (1)
- ・インスペック (1)
- ・エツキ (1)
- ・ソニー (3)
- ・ソニー教育財団 (1)
- ・ソフトバンク (1)
- ・ティ・ディ・シー (1)
- ・デュナミス (1)
- ・ドットジェイピー (1)
- ・ナノテム (1)
- ・ハリウコミュニケーションズ (3)
- ・ハード工業有限会社 (1)
- ・フジイコーポレーション (1)
- ・プレファクト株式会社 (1)
- ・ヤマダフーズ (1)
- ・全国学習塾協会 (3)
- ・公益社団法人セーブ・ザ・チルドレン・ジャパン (1)
- ・勝山酒造部 (1)
- ・及源鋳造株式会社 (1)
- ・大武・ルート工業 (1)
- ・太白少年少女発明クラブ (1)
- ・宮城の新聞 (0)
- ・宮城県中小企業家同友会 (1)
- ・宮城県産業人クラブ (0)
- ・宮城県職業能力開発協会 (1)
- ・宮城県酒造組合 (2)
- ・工藤電機 (2)
- ・平孝酒造 (1)
- ・応用物理学会 (2)
- ・新東総業株式会社 (1)
- ・日刊工業新聞社 (7)
- ・日本アンドロイドの会 (1)
- ・日本技術士会 (2)
- ・日本私立大学団体連合会 (1)
- ・日本農芸化学会東北支部 (1)
- ・日本IBM (3)
- ・日東イシダ (1)
- ・有限会社 柏崎青果 (1)
- ・東京エレクトロン宮城 (1)
- ・東北ニュービジネス協議会 (1)
- ・東北活性化研究センター (3)
- ・東北経済連合会 (1)
- ・東北電力 (2)
- ・東北電子産業株式会社 (1)
- ・東栄科学産業 (1)
- ・林精器製造 (1)
- ・株式会社三栄機械 (1)
- ・株式会社悠心 (1)
- ・河北新報 (1)
- ・神田産業株式会社 (1)
- ・秋田化学工業 (1)
- ・笹氣出版印刷 (1)
- ・米鶴酒造 (1)
- ・萩野酒造 (1)
- ・農芸化学会 (1)
- ・遠藤工業 (1)
- ・鈴木製作所 (1)
- ・阿部蒲鉾 (1)
- ・阿部蒲鉾店 (1)
- ・鳴子の米プロジェクト (1)
- ・NECトーキン (1)
特別企画 「宮城の塾」
![]() |
学習塾から見る 宮城の教育の「今」 塾選びに一役 |

![]() |
【科学って、そもそもなんだろう?】 若手研究者座談会「地震学×情報科学の融合で得られたもの」 2024.09.16 |
![]() |
【科学って、そもそもなんだろう?】 地震の発生予測に挑む(京大防災研の西村卓也さん・京大名誉教授の平原和朗さんに聞く) 2023.01.26 |
![]() |
【社会って、そもそもなんだろう?】 【同窓生に聞く#01】中鉢良治さん(元ソニー社長、産総研最高顧問)がリアルに感じていることって、何ですか? 2022.10.27 |
![]() |
【科学って、そもそもなんだろう?】 地震学×情報科学の融合で、目指すは天気予報の地震版 2022.04.13 |
![]() |
【社会って、そもそもなんだろう?】 「仙台の地形と水との関わり」~地形から見る仙台の過去・現在・未来~ 2022.03.02 |
![]() |
【科学って、そもそもなんだろう?】 青井真さん(防災科学技術研究所)に聞く:<東日本大震災から10年>東北地方太平洋沖地震が起きて、地震研究はどう変わった? 2021.11.11 |
記者ブログ
![]() |
ひとり新聞社「宮城の新聞」の大草よしえが衆院選に立候補 2021.10.19 |
![]() |
最近の活動は「Twitter」に移行しました 2019.11.01 |
![]() |
【追記】テレビ朝日「モーニングバード」スタジオ生出演&iCAN'15世界大会(アラスカ)世界第1位! 2015.06.19 |
![]() |
2014年の振り返りと、2015年の抱負 2015.01.05 |
![]() |
平成25年度を振り返りました・・・。 2014.04.02 |
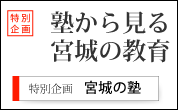
![]() |
中野塾(泉中央・北高森) |
![]() |
ひのき進学教室(泉中央・長命ヶ丘・八幡教室・上杉教室) |
![]() |
夢学館(東照宮・福室) |
![]() |
早稲田育英ゼミナール(泉中央) |
![]() |
ソーメック個別学習院(若林区、太白区、泉区に6教室) |
![]() |
明和塾(北山・八木山) |
![]() |
JUKU ペガサス仙台南光台教室(南光台南) |
アクセスランキング
- 【宮城の塾】 宮城の塾 仙台市を中心とした学習塾・幼児教室・進学塾の特集
- 世界中の研究者が憧れる研究拠点へ/東北大学WPI-AIMR本館竣工記念式典/科学って、そもそもなんだろう?
- [vol.1] 第1回宮城の日本酒を楽しむ会/社会って、そもそもなんだろう?
- 「仙台の地形と水との関わり」~地形から見る仙台の過去・現在・未来~/社会って、そもそもなんだろう?
- 宮城県仙台第一高等学校/教育って、そもそもなんだろう?
- 【宮城の塾】 ひのき進学教室(泉中央本部教室・八幡町教室・上杉教室・五橋教室・長町教室・愛子教室・吉成教室・大和町教室、他)
- 地震の発生予測に挑む(京大防災研の西村卓也さん・京大名誉教授の平原和朗さんに聞く)/科学って、そもそもなんだろう?
- 【宮城の塾】 JUKU ペガサス仙台南光台教室
- 【宮城の塾】 質問できます!/宮城の塾|宮城の新聞
- 【宮城の塾】 明和塾(北山教室・八木山教室)